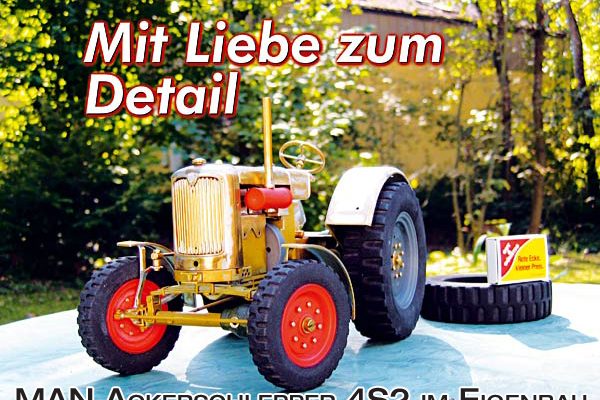
Mit Liebe zum Detail – MAN Ackerschlepper 4S2
Filigranarbeit ist für Funktionsmodellbauer nicht nur Anspruch, sondern oft auch notwendige Realitœt, um dem gesteckten Ziel nœher zu kommen. Aber nicht nur im originalgetreuen Nachbau von funktionierenden Modellen, auch im Standmodellbau wird sehr viel Wert auf die perfekte Detailwiedergabe der Originale gelegt. So ist der folgende Bericht des Ackerschleppers auch für fahrende, baggernde, transportierende, löschende und hebende Modellbauer eine hilfreiche Quelle für interessante Umsetzungsmöglichkeiten.
Der Eigenbau eines Modells nimmt viel Zeit in Anspruch, viele Wochen, sogar mehrere Monate. Da fällt die Entscheidung bei der Wahl eines neuen Modells keineswegs leicht. Viele Vorbilder erscheinen attraktiv – doch warum fällt die Entscheidung ausgerechnet auf den Ackerschlepper?
Modellauswahl
Die letzten Modelle, die ich gebaut habe, waren ein US-Militärlaster M 35 A2, ein Willys Jeep und den Unimog U 140 mit Sichtkanal. Alle diese Fahrzeuge haben eines gemeinsam: Sie sind als klassische Nutzfahrzeuge mit separatem Rahmen, von dem ausgehend das Fahrzeug aufgebaut ist, konzipiert. In einer Zeitschrift hatte ich ein Foto des MAN-Traktors 4S2 aus den 50er-Jahren gesehen. Dieser gefiel mir auf Anhieb so gut, dass ich entschied, diesen Traktor im Maßstab 1:14 zu bauen.
Nach Kriegsende nahm die Maschinenfabrik Augsburg-Nürnberg (MAN) 1949 die Fertigung der als „Ackerdiesel“ bezeichneten Schlepper wieder auf. Zwischen 1957 und 1960 baute MAN als stärksten Schlepper den Typ 4S2. Dieser war in rahmenloser Blockbauweise konzipiert, ausgestattet mit einem 50 PS starken, wassergekühlten Vierzylinder-Viertakt-Dieselmotor und Allrad-Antrieb.
Am Anfang steht die Zeichnung
Das Vorbild, ein Schuco-Modell in 1:43, war schnell besorgt. Als erstes habe ich Zusammenstellungszeichnungen mit den Hauptabmessungen in 1:14 angefertigt, konventionell mit Tusche und Transparentpapier. In der Regel reicht ein DIN-A3-Zeichenbrett völlig aus. Die Abmessungen wurden mit einer Schieblehre vom 1:43-Modell abgegriffen und entsprechend umgerechnet. Ich halte es für wenig zweckmäßig, bereits am Anfang alle Detailzeichnungen anzufertigen. Oftmals ergibt sich während des Baufortschritts die Notwendigkeit für Modifikationen einzelner Bauteile, manche Konstruktionen erweisen sich als ungeeignet und müssen völlig neu überlegt werden.
Reifen und Felgen
Als erstes waren die Reifen dran; bei einem Traktor zwangsläufig unterschiedliche für vorne und hinten. Ich hatte mir vorgenommen, entsprechend dem Vorbild hinten zweiteilige Felgen zu bauen, vorne einteilige. Die vorderen wurden nach bewährtem Schema erstellt. Als Material verwendete ich PVC, welches ich in Form von Rundstäben mit unterschiedlichen Durchmessern in meinem Lager vorhalte. Von diesem Stangenmaterial wurden zwei Scheiben abgesägt und auf der Drehmaschine in die gewünschte Form gebracht. Analog wurde bei den hinteren Felgen vorgegangen, nur bestehen diese jeweils aus einem Außenring (Felgenbett) und einem Innenteil. Beide sind als Passung konzipiert; das Innenteil liegt an einer Drehkante des Außenrings an. Beide Felgen weisen eine Reihe von Bohrungen auf, welche symmetrisch auf verschiedenen Radien angeordnet sind. Um diese Bohrungen einzubringen, bieten sich Fräsmaschine und Teilapparat an. Mit der gleichen Anordnung wurden die inneren Felgenbauteile bearbeitet, um die vier Ausnehmungen am Außenradius anzubringen. Dazu wurde der X-Y-Vorschub des Kreuztisches entsprechend eingesetzt. Die Erfahrung hat gezeigt, dass es manchmal günstig ist, die Fräsarbeiten vor den Dreharbeiten am Rohling vorzunehmen.
Die Reifen wurden aus Hartgummi angefertigt. Da das Gummi als Plattenmaterial vorlag, musste zunächst ein entsprechend großes Quadrat mit dem Messer oder einer Säge ausgeschnitten werden. Mit der Drehmaschine oder der Fräsmaschine plus Teilapparat erfolgten die weiteren Arbeitsschritte. Da die hinteren Reifen im Endzustand einen Außendurchmesser von 112 Millimetern aufweisen, wurde zur Erstellung des Reifenrohkörpers (Zylinderform) die Fräsmaschine eingesetzt. Um den Rohkörper auf Endmaß zu bringen, wurde die Drehmaschine bemüht.
Reifen ohne Profil sehen etwas jämmerlich aus – profillos. Das Modell sollte das typische Profil von Traktorreifen bekommen. Ich investierte viel Zeit in die Vorbereitung: Der Teilapparat wurde im entsprechenden Winkel zur Y-Achse am Kreuztisch der Fräse fixiert. Zusätzlich wurde eine Vorrichtung gebaut, um den Teilapparat in entsprechender Schieflage befestigen zu können, doch alle Versuche scheiterten. Ich musste einsehen, dass gleichzeitig die X-, Y-, Z-Achse und zusätzlich die Drehbewegung des Teilapparats angesteuert werden müssen, um ein vorbildgetreues V-Profil herstellen zu können. Über die notwendigen motorischen Stellantriebe verfügt meine Fräsmaschine nicht. Das Ergebnis war etwas ernüchternd, der Testreifen war durch die diversen Fräsversuche Ausschuss geworden; ein neuer musste angefertigt werden. Darüber hinaus musste ich mich damit abfinden, dass mein Modell nun auf Reifen steht, welche lediglich über Stollenprofil verfügen. Mit der Herstellung dieser Reifen habe ich inzwischen einige Erfahrung. Einfache Vorrichtungen wurden angefertigt, um die Reifen im Teilapparat so einspannen zu können, dass Stirnfräser und Frässpindel nicht mit dem Teilapparat kollidieren. Ist der Teilapparat justiert und befestigt, das Werkstück zentriert und alle Nullstellungen fixiert, wird das Profilfräsen zu einer (zeitintensiven) Routineangelegenheit. Für die vier Traktorreifen waren immerhin 240 Axialvorschübe und ebenso viele Winkeldrehungen notwendig. Da kann es schon mal passieren, dass bei nachlassender Konzentration eine falsche Umdrehung am Vorschub zu einem totalen Ausschuss des Bauteils führt – Künstlerpech!
Rahmenlose Blockbauweise
Die wesentlichen Bauteile des Traktors sind der Getriebe- und Motorblock. Dazwischen sitzt das Kupplungsgehäuse und vorne am Motorblock der Vorderachsträger. Getriebe- und Motorblock wurden aus Messingblechen zusammengelötet. Da beide Komponenten im weiteren Baufortschritt eine Reihe von Bohrungen aufnehmen müssen, wurde ein Messingblech von 0,6 Millimetern Dicke gewählt; ansonsten reicht ein 0,3- oder 0,4-Millimeter-Blech völlig aus. Beide Komponenten wurden nach oben offen gestaltet, um notwendige Einbauten unterbringen zu können. Das Kupplungsgehäuse wurde als Drehteil aus PVC angefertigt und mit Getriebegehäuse und Motorblock verschraubt. Der Vorderachsträger ist ebenfalls ein gelötetes Hohlprofil, welches jedoch so ausgeführt wurde, dass es über ein zentrales Lager verfügt. Dieses nimmt die Vorderachse auf und ermöglicht gleichzeitig die Pendelbewegung der Vorderachse. Der Vorderachsträger wurde an der Stirnseite des Motorblocks angeschraubt.
Vorder- und Hinterachse
Die Hinterachse ist recht einfach herzustellen. Sie besteht aus einem Messingrohr von sechs mal ein Millimeter. Um die Hinterräder befestigen zu können, werden links und rechts Formstücke (vier Millimeter Durchmesser mit kurzem M4-Gewindestück) eingepasst, vernietet und verlötet. Das Achsrohr wird durch zwei Bohrungen in das Getriebegehäuse gesteckt und unsichtbar im Inneren verschraubt. Um die äußere Kontur der Originalhinterachse nachzuempfinden, wurden entsprechend geformte Drehteile über das Sechs-Millimeter-Rohr geschoben. Zusammen mit den Bremstrommeln werden so die Hinterräder in ihrer axialen Position fixiert. Den äußeren Abschluss bilden eine gedrehte Messingscheibe und eine M4-Mutter. Um die so genannte Ackerschiene an der Hinterachse befestigen zu können, wurden entsprechende Gewinde in das Achsrohr gebohrt.
Die Vorderachse ist etwas aufwändiger: Sie ist gefedert, pendelnd gelagert, wird ebenfalls angetrieben und verfügt deshalb über ein Differenzial. Wegen der Pendellagerung der Vorderachse sind zusätzlich Längslenker vorhanden, welche die Kräfte auf die Vorderachse in Fahrzeuglängsachse aufnehmen. Die Vorderachse besteht – analog zur Hinterachse – im Wesentlichen aus einem Acht-mal-Ein-Millimeter-Messingrohr, auf welches das seitlich versetzte Differenzialgehäuse als Drehteil aufgeschoben und dort fixiert wurde. An den beiden Enden des Messingrohres wurden die Lager für die Achsschenkel montiert. Diese wurden aus einem kurzen Stück U-Profil (12 x 8 x 1 Millimeter) gefertigt. Der Achsschenkel besteht ebenfalls aus einem Stück U-Profil – jedoch mit den Abmessungen zehn mal sechs mal ein Millimeter – welches so lang gewählt wurde, damit dieses Bauteil gleichzeitig die Spurstangenlager aufnimmt. Eine Besonderheit bei dem MAN-Schlepper: Die Spurstange ist wegen des Allradantriebs vor der Vorderachse positioniert. Dies hat zur Folge, dass der Abstand zwischen den beiden Spurstangenlagern größer sein muss als der Abstand zwischen den Achsschenkellagern. Nur so ergibt sich die korrekte Lenkgeometrie. Die Verbindung zwischen Vorderachsrohr und quer liegender Blattfeder muss die Längenänderung des Federpakets beim Einfedern aufnehmen. Diese Verbindung wird über zwei H-förmige Zwischenstücke hergestellt, welche aus dem Vollen gearbeitet wurden. Die Blattfeder selbst war in ihrem früheren Leben Teil eines Laub-Rechens. Die Federstahlzacken dieses Rechens passten von den Abmessungen her in etwa für das Federpaket. Die Bearbeitung ist nicht problemlos, da sich Federstahl nur sehr widerwillig schneiden, sägen und bohren lässt. Mit Hochleistungsfräsern ist mir die Bearbeitung gelungen: einkürzen, schmälern und die notwendigen Bohrungen einbringen. Um die Pendelbewegung der Vorderachse zu ermöglichen, ist das Federpaket mittig drehbar gelagert; ein zweites Lager am hinteren Ende des Motorblocks nimmt die Längslenker (Zug-Druckstäbe) auf.
Lenkung
Wegen des geringen Platzbedarfs und der speziellen Traktorgeometrie beschloss ich, als Lenkgetriebe eine Schneckenrad-Ritzel-Kombination einzubauen. Was mich zögern ließ war der Umstand, dass ich den Schneckenradsatz nicht selbst herstellen konnte und ich entgegen meinen Grundsätzen ein Kaufteil von Conrad Electronic einsetzen musste. Als Untersetzung wurde ein Zahnrad mit 20 Zähnen gewählt. Die Schnecke wurde auf der Lenksäule fixiert, zwischen der oberen und unteren Lenksäulenlagerung. Das Ritzel wurde im Getriebegehäuse verstaut. Bald stellte sich heraus, dass das Spiel bei dieser Art von Lenkgetriebe relativ groß ausfiel. Aus dem Grund wurde die Lagerung des Ritzels modifiziert: Das Ritzel wurde in einen Schlitten eingebaut, der axial verschiebbar die Einstellung des Flankenspiels zwischen Schnecke und Zahnrad erlaubt. Das Lenkrad selbst ist ein Bauteil, welches aus einem Messingflachstab (3 x 40 Millimeter) gedreht wurde. Die Nabe wurde mit Hilfe der Drehmaschine geformt; zuvor bereits mit Hilfe der Fräse mit zwei senkrecht zueinander stehenden 1,5-Millimeter-Bohrungen zur Aufnahme der Speichen versehen. Für derartige Bohrungen empfiehlt sich die Verwendung der Fräsmaschine und eines Stirnfräsers. Der Kreuztisch der Fräse erlaubt ein sehr genaues Positionieren. Um die Nabe möglichst zentrisch mit dem Lenkradkranz zu verbinden, wurde eine Vorrichtung angefertigt, welche Lenkradkranz und Nabe mit den bereits verlöteten vier Speichen während des Zusammenfügens formschlüssig aufnimmt.
Nachdem die Hebel und die Verbindungselemente zur Anlenkung der Vorderachse fertig gestellt waren, musste ich feststellen, dass die Lenkung verkehrt herum funktionierte. Wenn man das Lenkrad nach rechts drehte, schlugen die Vorderräder nach links ein. So etwas war mir bisher noch nie passiert! Was tun? Entweder das Lenkgetriebe umbauen oder aber ganz einfach: Das Lenkungsgestänge von der linken Traktorseite auf die rechte verlegen. Ich entschied mich für die einfache, allerdings nicht dem Original entsprechende Lösung.
Frontpartie und Kühlergrill
Der hier beschriebene Schlepper kann und will seine Zugehörigkeit zur MAN-Familie nicht leugnen. Allzu sehr ähneln sich die Frontpartien von Lastwagen und Traktoren der Nachkriegsära. Beim Original verfügt der Kühlergrill über zirka 30 vertikale Streben; beim 1:43-Modell wurde die Anzahl der Streben auf etwa die Hälfte reduziert. Bei meinem Modell wurden ebenfalls nur 15 dargestellt, das passte bei einer Strebendicke von einem Millimeter und einer Kühlgitterbreite von zirka 30 Millimetern. Die Frontpartie besteht bei meinem Modell aus drei Einzelkomponenten: Der äußeren Blechhaut, dem Grilleinsatz und dem eigentlichen Kühler. Alle diese Komponenten wurden als Kastenprofile (Volumenelemente) angefertigt. Bei der Herstellung war das Augenmerk von Anfang an darauf gerichtet, dass die endgültige Frontpartie wesentlich von der elfenbeinfarbenen Umrandung des Kühlergrills geprägt ist. Deshalb war eine Konstruktion zu überlegen, welche es relativ einfach ermöglicht, diese Lackierung umzusetzen. Die komplett sichtbare Frontpartie wurde zunächst aus einem vorderen Abschlussblech gefertigt, auf welches die erhabene Kühlerfassung (1-x-1-Millimeter-Profil) aufgelötet wurde. Nach Abschluss der Lötarbeiten wurde das Blech im Innern der Kühlerfassung durch Feilen sorgfältig entfernt. Als Nächstes wurde ein Bauteil (Kastenprofil) gefertigt und von hinten in die Frontpartie eingeschoben. Es gibt exakt die Krümmung der Front wieder. Auf das konvexe Frontblech dieses Bauteils wurden die Streben (Ein-Millimeter-Messingdraht) eine nach der anderen äußerst vorsichtig aufgelötet. Die Streben wurden mit der Feile derart eingekürzt, dass sie exakt in die ausgefeilte Öffnung der Frontpartie passten. Auf diese Weise sind nun die erhabene Kühlerfassung sowie die Kühlerstreben auf einer Ebene. Als drittes Bauteil wurde der eigentliche Kühler angefertigt, der ebenfalls von hinten in die Frontpartie eingepasst wurde. Dieses kaum sichtbare Bauteil dient der Auflagerung der Motorhaube.
Interessante Einzelbauteile
Die hinteren Kotflügel sind optisch recht präsent, weshalb eine exakte Formgebung angebracht erschien. Um dies zu erreichen, wurden Schablonen angefertigt, an welche die gekrümmten Bleche während der Herstellung angeheftet wurden. Die fertigen Bauteile verfügen mit den Abschlussblechen und den gerundeten, verstärkten Außenrändern über ausreichend Stabilität, sodass die Montagehilfen wieder entfernt werden konnten. Der Fahrersitz dürfte im Original als eine einschalige, tief gezogene Blechschale gefertigt sein. Wie sollte diese filigrane Blechstruktur modelliert werden? Ein Holzmodell herstellen und das Blech treiben? Derartiges habe ich bisher nicht ausprobiert; ich weiß jedoch, dass sich die zur Verfügung stehenden Messingbleche nur äußerst unwillig dreidimensional formen lassen. Vorgegangen wurde derart, dass ausgehend von einem mittigen, einfach gekrümmten Blechstreifen durch vorsichtigstes Anlöten weiterer kleiner Blechstreifen die endgültige Kontur erreicht wurde. Die umgebogenen Ränder des Originals wurden durch Anlöten eines umlaufenden Ein-Millimeter-Drahtes simuliert. Um zu einem zufrieden stellenden Ergebnis zu gelangen, wurden diverse Schablonen benutzt. Viel überflüssiges Lötzinn musste in mühsamer Handarbeit abgeschabt werden.
Die Frontscheinwerfer sind zunächst unscheinbare Kleinbauteile, doch erfordern auch diese eine gründliche Planung, wenn sie selbst angefertigt werden sollen. Die Scheinwerferge-häuse wurden aus Kunststoff hergestellt. Ein 15-Millimeter-PVC-Rundstab von etwa 100 Millimetern Länge wurde an den beiden Rändern auf das Außenmaß der Scheinwerfer (zwölf Millimeter) abgedreht. Anschließend wurde die endgültige Form der Scheinwerfer (Vorderseite) auf der Drehmaschine hergestellt. Zusätzlich musste eine zentrale Sacklochbohrung von sechs Millimetern Durchmesser angefertigt werden, diese wird für die endgültige Bearbeitung der anderen Hälfte des Scheinwerfers benötigt. Der Rundstab mit den beiden bearbeiteten Enden wurde anschließend mit Hilfe der Fräsmaschine mit je einer seitlichen Bohrung von 1,5 Millimetern Durchmesser versehen. In die Bohrungen wurden M2-Gewinde geschnitten. Die Scheinwerfer sind mit M2-Schrauben an der Frontpartie befestigt. Nach Absägen der beiden Enden vom Rundstab wurde in die Sechs-Millimeter-Bohrung dieser Formstücke eine Sechs-Millimeter-Achse eingepresst. Diese Achse wurde in die Drehmaschine eingespannt und die Endbearbeitung (Halbkugelform) des Bauteils vorgenommen. Die Scheinwerfer-Gläser wurden aus Fünf-Millimeter-Plexiglas hergestellt. Mit der Fräsmaschine wurden zunächst exakte Quadrate (12 x 12 Millimeter) gefertigt. Diese wurden im Vierbacken-Drehfutter so eingespannt, dass sie aus dem Drehfutter etwa zur Hälfte herausragten und ein Abdrehen des Quadrats auf sechs Millimeter Durchmesser möglich wurde. Anschließend wurden diese Bauteile umgedreht eingespannt und auf das Endmaß der Gläser abgedreht. Die Sechs-Millimeter-Andrehung passt nun exakt in das Sackloch im Scheinwerfergehäuse.
Die seitlichen Begrenzungsleuchten auf den Kotflügeln erlebten eine etwas andere Entstehungsgeschichte als die Hauptscheinwerfer. Ausgangsmaterial war ebenfalls ein PVC-Rundstab, der in diesem Fall an den Enden auf sieben Millimeter abgedreht wurde. Jedoch wurde nun zuerst die Halbkugelkontur angedreht. Anschließend wurde in der Drehmaschine eine koaxiale 1,5-Millimeter-Bohrung hergestellt und anschließend mit einem M2-Gewinde versehen. Dieses Gewinde ist notwendig, um hinterher das Bauteil mit Hilfe einer Vorrichtung und einer M2-Schraube zur Bearbeitung der zweiten Leuchtenhälfte ins Drehfutter einspannen zu können. Geplant war, die Begrenzungsleuchten mit einer M2-Schraube direkt an den Kotflügeln zu befestigen. Die Kotflügel weisen an dieser Position einen Winkel von 54 Grad zur Horizontalen auf. Um diesen Winkel bei den Gewindebohrungen zu erreichen, wurde der Rundstab mit den angedrehten Halbkugel-Enden analog zu der Prozedur bei den Hauptscheinwerfern in die Fräsmaschine eingespannt. Nun jedoch musste der Fräskopf um 54 Grad geschwenkt werden, um die Bohrungen mit dem Pinolenvorschub anzubringen.
Bis zum fertigen Modell waren noch Dutzende von Einzelkomponenten zu fertigen: Der Beifahrersitz mit einem Ein-Millimeter-Geländer, die Radmuttern als kurze Zylinderstifte, Anlasser, Lichtmaschine, Kühlerventilator, das Abgassystem (so einfach es aussieht, es besteht aus insgesamt 16 einzelnen Drehteilen), die Brennstoffzufuhr und noch einiges mehr.
Spachteln, Grundieren, Lackieren
Diese Tätigkeiten nehmen im Vergleich zur Komponentenfertigung einen relativ geringen Zeitraum in Anspruch. Dies ist einerseits erfreulich – endlich geht das Projekt zu Ende – andererseits ist der Erfahrungsschatz entsprechend gering. Mir geht es so, dass bei diesen Arbeiten immer wieder unerwartete Effekte auftreten. Diesmal hatte ich zum Spachteln eine neue Spachtelmasse aus dem Baumarkt. Als nach ausreichender Trocknungszeit ein Haftgrund aufgespritzt wurde, kam es zur Auflösung der Spachtelmasse. Ein Lackierermeister in einer Autolackiererei wurde um Rat gefragt. Dieser meinte, dass der Zweikomponenten-Haftgrund so aggressiv sei, dass dieser die Spachtelmasse angreift. Er empfahl die Verwendung einer Zweikomponenten-Spachtelmasse. Dieser Spachtelmasse werden drei Prozent Härter beigemischt. Nach dem Mischen verbleiben nur etwa drei Minuten Zeit zum Verarbeiten, dann setzt der Aushärtevorgang ein. Diese Spachtelmasse hat sich bewährt. In der Autolackiererei wurden gleichzeitig die typischen MAN-Farben gemischt. Dies war etwas schwierig, da die etwa zwei Dutzend Farbaufnahmen in dem Bildband „Deutsche Traktoren, 1920-1970“ (von Udo Paulitz, HEEL Verlag GmbH) eben so viele unterschiedliche Grüntöne aufwiesen. Geeinigt haben wir uns auf ein Resedagrün und eine helle Elfenbeinfarbe für die Felgen.
Typisch für die MAN-Traktoren der Nachkriegszeit ist sowohl die Gestaltung der Frontpartie als auch die Farbgebung der Umrandung des Kühlergitters. Diese wurde grundsätzlich in der Farbe der Felgen lackiert. Nun hatte ich bereits bei der Konzeption der Frontpartie darauf geachtet, dass eine entsprechende Zweifarb-Lackierung möglich ist. Um dies zu bewerkstelligen, wurden die Bauteile Kühler und Kühlergitter aus der Frontpartie entfernt, sodass eine gähnende Öffnung entstand. Für den Farbauftrag wurde eine spezielle Farbrolle angefertigt. Diese funktioniert wie handelsübliche Farbrollen, die zum Weißeln und Lackieren verwendet werden. Allerdings beträgt der Durchmesser der Rolle nur 15 Millimeter, die Breite knapp 20 Millimeter. Hergestellt ist diese Rolle aus PVC. Die Farbe wird aufgetragen, indem die Oberfläche der Rolle mit einer dünnen Farbschicht versehen wird, welche durch Abrollen auf die Kühlerumrandung übertragen wird.
Nach den Lackierarbeiten war das Modell endlich vitrinentauglich! Für die Zukunft bestehen noch viele Pläne, manches ist zu ertüchtigen und zu verbessern, unter anderem steht das Anfertigen von Schriftzügen und Firmenlogos mit Fotoätztechnik oder Folienverfahren an. Parallel mit der Endmontage des MAN-Traktors laufen die Überlegungen zu einem Anschlussprojekt. Es könnte ein Kleinlaster der Wirtschaftswunderzeit werden.