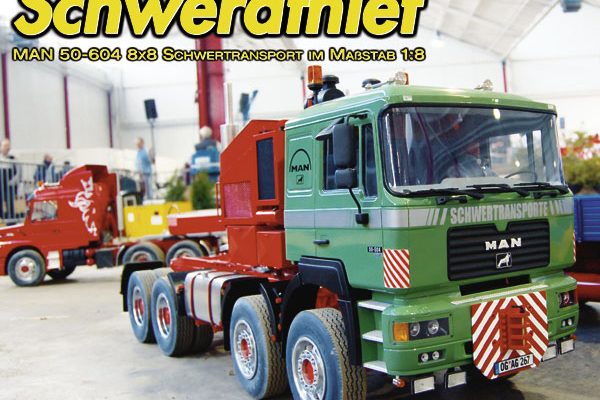
Schwerathlet – MAN 50-604 8×8 Schwertransport
Ein Schwertransport-Modell von MAN zu bauen, war schon immer mein Ziel. Besonders reizte mich der MAN-8×8-Vierachser. Nach langer Suche, vielen Telefonaten und Briefen wurde ich fündig. In einer MAN-Filiale in meiner Nähe konnte ich den Originalplan im Maßstab 1:10 vom Fahrgestell 50-604 8×8 in der Grundversion bekommen.
Von diesem Typ gibt es leider nicht sehr viele. Laut MAN wurde sogar jedes Fahrzeug individuell nach Kundenwünschen aufgebaut. Als Vorbild wählte ich ein Fahrzeug des Transportunternehmens Felbermayr, da mir der hintere Aufbau sehr gut gefiel. In der Zwischenzeit besorgte ich auf der Sinsheimer Modellbaumesse wichtiges Aufbaumaterial wie die Räder, Felgen und Achsen von Veroma sowie das MAN-F2000-Fahrerhaus von Schink’s Modellbau.
Fahrwerk
Zuerst fertigte ich Skizzen vom Rahmen an, umgerechnet in den Maßstab 1:8. Die Zeichnungen dienten gleichzeitig als Schablonen. So konnte ich auch relativ leicht die typische „Fischbauchform“ biegen. Für den Hauptrahmen wurde Stahl im U-Profil wie beim Original, jedoch maßstabsgetreu in 35 x 10 x 100 Millimeter, verwendet. Zuerst wurden die vielen Bohrungen und das Gewinde geschnitten. Zusätzlich gibt es Querstreben aus Aluprofil. Für die Aufnahme des Fahrwerks und der Querstreben wurden die Teile mit M3-Inbus-Schrauben verbunden, um eine sehr gute Stabilität zu erreichen. Ich sägte und feilte alles von Hand. Für die vordere Achse verwendete ich Achs-Aufhängungen mit Blattfedern und passte sie dem Rahmen an, zusätzlich drehte ich noch vier Stoßdämpfer an, um dem Vorbild näher zu kommen. In der Zwischenzeit fertigte ich Skizzen für die Pendelachse und ließ sie fräsen, da ich selber keine große Maschine dafür besitze. Für die Blattfeder verwendete ich Federstahl und legte dazwischen Glasfaserstreifen zur Verstärkung. Zum Verbinden des Pendelsystems und der Achse nahm ich M5-Kugelgelenke. Momentan wird das Modell aus Kostengründen nur über drei Achsen angetrieben. Der Antrieb enthält zwei hintere Differenziale mit Außengetriebe. Das dritte befindet sich in der angetriebenen Vorderachse – ebenfalls mit Außengetriebe – und die vordere Achse ohne Antrieb wurde selbst hergestellt, um diese zu späterer Zeit umzubauen.
Lenkung & Antrieb
Danach wurde die Lenkungs-Geometrie geplant und aufgebaut. Natürlich lief nicht alles so wie geplant. Zuerst kamen für jede Lenkachse zwei auf 6 Volt umgebaute Jumboservos mit zirka 27 Kilogramm Stellkraft zum Einsatz, sodass man wenigstens während der Fahrt lenken konnte. Beim nächsten Messetermin fand ich aber einen sehr starken Getriebemotor, der umgebaut wurde, sodass er wie ein Servo funktionierte. Ich verwendete zudem einen 10-Ampere-Fahrtregler und schloss das Poti parallel zum Motorhebel an. So überstand der Truck sehr lange Testfahrten und jedes Gelände einwandfrei und ohne Probleme. Als Antrieb verwendete ich einen sehr starken Bosch-Elektromotor für 12 Volt mit 6.500 Umdrehungen pro Minute und verband ihn mit einem Zwischenverteiler-Getriebe (1:3). Durch die Untersetzung des Differenzials entstand ein optimaler und kraftvoller Antrieb. Das Ganze wurde von mir mit Stahlkardangelenken und beweglicher Welle aus Messingvollmaterial hergestellt, sodass alles funktioniert wie beim Original. Lediglich die Hinterachse bestückte ich mit Bremszylinder- und Bremshebel-Attrappen.
Detailarbeit
Anschließend schnitt ich aus einem MAN-Katalog das Logo aus und klebte es auf ein Stückchen Alu. In mühsamer Arbeit sägte ich es aus und feilte die Konturen. Danach baute ich mir eine Form und goss das Logo aus Kunststoff. Nun kam das Fahrerhaus an die Reihe. Zuerst wurde alles grob geschliffen und, wo nötig, gesägt und dann grob an das Fahrgestell eingepasst. Am Fahrerhaus selber wurde von außen der Kühlergrill eingepasst und von innen geschraubt. Die Türen schnitt ich nicht auf, da ich keinen Wert darauf lege und auch eine höhere Stabilität erreichen wollte. Beim Vorbild-Fahrzeug handelt es sich um eines mit Allradantrieb, daher liegt das Fahrerhaus viel höher als das konventioneller Fahrzeuge. Das heißt, dass ich die mitgelieferten Kotflügel ändern musste. Ein weiteres Problem: Das Fahrerhaus soll federn und kippen. Zuerst wurde der Fahrerhausboden eingepasst und festgeschraubt. Für eine weiche vordere Federung verwendete ich 3-Millimeter-Federstahl, gebogen in U-Form. Zudem verbaute ich Scharniere und kleine Stoßdämpfer, die wie beim Original am Rahmen befestigt wurden. Natürlich musste alles so oft verstellt und getestet werden, bis es funktionierte.
Innenraum
Nachdem von außen alles fertig war, kümmerte ich mich um die Inneneinrichtung. Da sich die Türen nicht öffnen lassen, wollte ich zumindest die Fenster bedienen können (von Hand runter- und hochziehen). Dazu verwendete ich einen Rahmen aus einem Messing-U-Profil für die Führung der Scheibe. Lediglich die Türen wurden von innen mit Wurzelholzfurnier und Kunststoff verkleidet und anschließend verschraubt. Zum Schluss wurde das Fahrerhaus nach getaner Arbeit im Farbton Rasengrün lackiert. Inzwischen fertigte ich die restliche Innenausstattung. Das Armaturenbrett wurde gleich mit Beleuchtung und Leuchtdiode für die Anzeige bestückt, um diese später funktionsfähig zu machen.
Fassade
Nachdem das Fahrerhaus fertig war, überlegte ich, wie ich die Kotflügel herstellen sollte. Auf dem Markt gibt es leider keine große Auswahl, die dann auch noch hätte angepasst werden müssen. So beschloss ich, die Kotflügel selbst herzustellen. Nach langer Suche fand ich im Baumarkt ein Abflussrohr mit 160 Millimeter Durchmesser. Zuhause wurde es entsprechend von Hand auf die passenden Maße zurechtgesägt. Dann schnitt ich aus einer 3-Millimeter-Kunststoffplatte je zwei Bordwände pro Kotflügel und klebte alles mit UHU Allplast zusammen – wie geschweißt! Nachdem ich das Ergebnis beschliffen hatte, verklebte ich die Teile miteinander. Zum Schluss wurden die Kotflügel mehrere Male grundiert und in Schwarz lackiert. Die Arbeit hat sich letztlich gelohnt. Für die Halterung verwendete ich Messingrundmaterial in 6 Millimeter Dicke und bog nach dem Originalplan alles in Form. Anschließend befestigte ich die Kotflügel mit Kabelmanschetten. Das Fahrgestell fing an, Form anzunehmen und die Lust am Bauen wurde größer.
Anbauteile
Für den Kraftstofftank formte ich aus Holz einen Klotz. Darum bog ich ein ein Millimeter dickes Alublech und ließ nur die Seitenteile und die untere Seite frei. Anschließend wurden zwei Seitenwände aus 3 Millimeter dickem Alu geschnitten, die mit UHU Endfest am Tankrohbau verklebt wurden. Für die Unterseite baute ich einen Deckel, der mit vier Schrauben befestigt wurde. Die Oberseite wurde dann noch mit zwei Löchern für den Tankdeckel und den Spritschlauch versehen. Der Tank wurde anschließend nur noch geschliffen und poliert. Aufgrund der schönen Optik entschied ich mich gegen eine Lackierung. Aufgehängt wurde der fertige Tank mittels zweier Metallbänder mit Scharnieren und Gummiunterlagen, die wegen einer besseren Montage am Rahmen an zwei Alu-U-Profilen in L-Form befestigt wurden.
Der Batteriekasten entstand aus zwei Polystyrolplatten, die durch ein Scharnier miteinander verbunden sind. So ist also eine Öffnung möglich, um eventuell mal eine Batterienachbildung unterbringen zu können. Für die Luftkessel, die am vorderen linken Teil des Rahmens angebracht wurden, verwendete ich Alurohre mit 30 Millimeter Durchmesser. Die Deckel dafür entstanden aus Edelstahl-Rohrdeckeln aus dem Sanitärzubehör, die ich lediglich mit der Drehmaschine polierte. Das Resultat war erstaunlich. Um die Kessel zu befestigen, fertigte ich wiederum Metallbänder an und verband damit die Luftbehälter. Die Verbindung zum Rahmen geschah mittels eines U-Messingprofils, das ich zwischen die Kesselgruppe befestigte. So ist eine Demontage einfacher und auch das Lackieren funktioniert besser.
Aufbau
Jetzt wurde der Hilfsrahmen gebaut – so unkompliziert wie nur möglich. Zum Einsatz kamen Aluprofile aus dem Baumarkt. Die beiden Enden vom Rahmen sägte und bohrte ich nach dem Originalplan. Anschließend fräste ich seitlich Langlöcher für die Aufnahme der Querstäbe und verschraubte alles mit Senkkopfschrauben. Am Hauptrahmen wurde der Hilfsrahmen von oben verschraubt. Nachdem das Fahrgestell fertig war, begann ich mit dem Bau des Schwerlastturms. Es hatte sich erwiesen, dass dies das schwierigste Bauteil des ganzen Fahrzeugs ist. Dieses musste zudem sehr stabil gebaut werden, da der Fahrakku noch Platz darin finden sollte. Ich begann bei der Konstruktion mit einem Vierkantprofil aus Aluminium, weil es sich sehr gut verarbeiten lässt. Auch das stammte aus dem Baumarkt. Das Profil verklebte ich miteinander und – wo es nötig war – verschraubte ich es mit Inbusschrauben. Diese sind zwar nicht billig, vermitteln aber eine gewisse Wertigkeit und sehen einfach schön aus. Zum Verschließen des Aufbaus entstand ein Deckel aus Alu ohne Scharniere, um leicht den Akku wechseln zu können. Weiterhin verschraubte ich noch zwei Arbeitsscheinwerfer und eine Schubstange.
So ein großer Aufbau bietet viel Platz, um weitere Sonderfunktionen unterzubringen. Beispielsweise war es wichtig für mich, dass sich die Rundumleuchten so drehen wie am Original. Das war eine große Herausforderung. Wie auch sonst oft, klappt beim Modellbau nicht alles sofort. Aber anhand vieler Tipps und Ratschläge aus der Fachpresse und von Kollegen gelang es letzten Endes. Zuerst besorgte ich genügend transparente Deckel aus dem Kosmetikbereich. Die zwei besten Deckel versah ich mit selbstgedrehten Töpfen aus Messing und presste ein Kugellager in den oberen Bereich. Unten schob ich ein 5-Millimeter-Messingrohr ein, das als Halterung diente. Darin befand sich ein 4-Millimeter-Messingrohr, in dem ein Rohr mit 3 Millimeter Durchmesser zur Führung der Lampenkabel steckte. Am Ende des 4-Millimeter-Rohrs lötete ich eine selbstgedrehte Rollenscheibe. Beide Scheiben verband ich in einer Dreiecksform mittels eines Gummiriemens mit dem Getriebemotor. So funktioniert es sehr gut und absolut störungsfrei.
Dann bestückte ich den Rest vom Schwerlastturm mit einem Ersatzrad und einem Staukasten, in dem sich der Hauptschalter für die Elektrik befindet und zusätzlich noch Platz für den Luftkühlungsschalter und den Soundmodulschalter vorhanden ist. Die zwei Luftfilter drehte ich aus Aluvollmaterial und schraubte sie an die Aufbaurahmen mit Manschetten. An die linke Seite kam noch ein weiterer Kraftstofftank, der im Original einem Hydraulik-Motor Leben einhaucht. Für die zwei Auspuffe verwendete ich ein Alurohr mit einem Durchmesser von ungefähr 30 Millimeter und presste die beiden Teile mit Hilfe eines Schraubstocks in eine ovale Form. Anschließend klebte ich zwei Deckel vorne und hinten in die Rohre und schon hatte ich die Auspufftöpfe. An der oberen Seite der Rohre befestigte ich entsprechend dünnere Endrohre und unten verband ich den Auspuff mit Kupferrohren bis zum Fahrmotor. Später sollen hier auch einmal Rauchentwickler eingebaut werden.
Pritsche
Nachdem dies fertig war, sägte ich aus einer Voll-Aluplatte mit einer Dicke von 10 Millimeter eine Sattelkupplung. Eine selbst entwickelte automatische Verriegelung baute ich direkt darunter. An der vorderen Stoßstange befestigte ich eine Registerkupplung. Zur Ergänzung entstand für das Fahrzeugheck eine Anhängerkupplung, die aus Alu gedreht und von Hand gefräst wurde. Als Zapfen nahm ich Federstahl von 3 Millimeter Dicke und verband ihn mit einer Verriegelung aus Messing. Da ich schon immer ein Goldhofer-Modul mit Anhängerkupplung bauen wollte, musste ich für meinem MAN eine Ballastpritsche bauen und so ging es weiter. Die Pritsche entstand aus einer Aluplatte von 2 Millimeter Dicke und ich verschraubte sie außen mit einem Aluwinkelrahmen, um eine Bodendicke von einem Zentimeter zu erreichen. Unten setzte ich zwei Querstreben zur Verstärkung ein und mit Hilfe eines Alukantprofils verschraubte ich alles an die Hilfsrahmen.
Der obere Aufbau besteht aus zwei festen Bordwänden vorne und hinten sowie zwei beweglichen Seitenwänden. Die Bordwände baute ich aus Gewichtsgründen aus einer ein Millimeter dicken Aluplatte und einem U-Profil für die Kontur. Dies verklebte ich dann mit Endfest-Kleber in Sandwich-Bauweise. An die Seitenwände gehörten zudem noch zwei Karabinerverschlüsse und drei Scharniere. In jede Ecke der Pritsche verklebte ich noch vier Kantrohre zur Aufnahme des oberen Gestells. Der Pritschenboden wurde mit einer Holzplatte verschraubt. Oben drauf setzte ich einen größeren verkleideten Akku als Ballastgewicht, um mehr Masse auf die hintere Achse zu bringen und gleichzeitig längere Zeit fahren zu können.
Für die Lackierung musste ich lange überlegen. Mir gefiel der Rohbau sehr gut, aber ohne Lackierung konnte ich das Modell nicht fertig stellen. Beispielsweise mit dem Einbau der Elektrik und der Beschriftung musste ich warten. Nun hieß es wieder: ab in den Keller und alles zerlegen. In Frage kam nur ein schönes Rot, weil das zum grünen Fahrerhaus passen würde und so auch alle Details vom Rahmen besser zu erkennen sein würden. Der Zusammenbau der vielen Teile nach der aufwändigen Lackierung wäre mir fast nicht gelungen, aber zum Glück hatte ich alles im Bild festgehalten. Ich muss zugeben, dass das Modell lackiert viel realistischer aussieht als vorher und ich sehr froh bin, das getan zu haben.
Innenleben
Jetzt konnte ich mit der Elektronik beginnen. Ich verwendete ein Lichtmodul von Graupner, das ich auf eine mit Relais und Sicherung erweiterte selbst entwickelte Platine setzte, um eine bessere Leistung und eine Erweiterung an Funktionen zu erhalten. Ein Soundmodul von Graupner mit separatem Akku sowie ein sehr feinfühliger Fahrtregler mit ungefähr 100 Ampere Leistung sind ebenfalls im Modell verbaut. Ein SMD-Schalter von Conrad sorgt für die Funktion der Arbeitsscheinwerfer und der Rundumleuchten, die per Funk zu bedienen sind.
Ins Fahrerhaus baute ich ein Armaturenbrett mit Beleuchtung und den üblichen Signalleuchten. Eine Innenbeleuchtung mit externem Schalter ergänzte ich zusätzlich. Für die Beschriftung wählte ich keine originalgetreue Umsetzung. Das muss ja auch nicht unbedingt sein. Von einer Druckerei ließ ich die Beschriftung nach meinen Vorstellungen herstellen. Insgesamt sind für den Bau gut 2 Jahre vergangen. Genau habe ich die Bauzeit bewusst nicht gezählt, da es ja nun mal ein Hobby ist. Es gibt immer irgendetwas, was umgebaut oder ergänzt werden könnte. Das Modell fährt aber bis zum heutigen Tag sehr gut und störungsfrei – trotz des Gewichts von ungefähr 50 Kilogramm. Im Gelände vermisse ich ein bisschen die vierte angetriebene Achse, aber das hat noch Zeit. Mein Wunschtraum vom MAN-Vierachser war bis dahin keine leichte Aufgabe. Des Öfteren war ich verzweifelt und habe viel an Nerven eingebüßt. Aber wenn ich meinen MAN aufstelle und vorführe und die Begeisterung der Zuschauer mitbekomme, war kein Tag zu schade, an dem ich in meinen Keller stand und an meinem Traum gebaut habe.