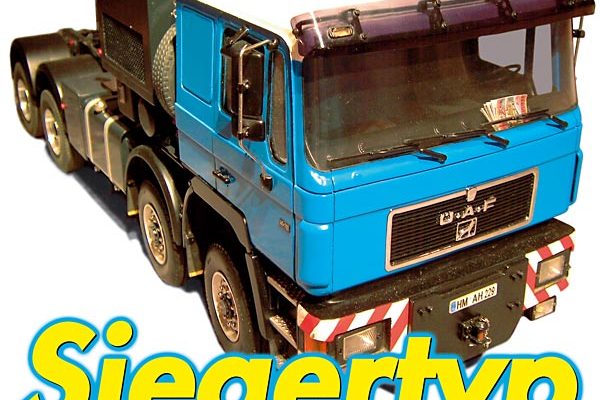
Siegertyp – ÖAF 48.792 – Bester Eigenbau bei der DM 2006
1990 fing ich mit der Suche nach einer Zugmaschine für mein erstes Modell an. Es war ein Tieflader, der nach einem Bauplan aus dem Hause Husemann entstanden war. Doch erst 1992 wurde ich auf der Internationalen Automobil Ausstellung (IAA) für Nutzfahrzeuge in Hannover vor der MAN-Halle fündig: Ich entdeckte den 48.792 von ÖAF. Dies war der Beginn einer innigen Beziehung, die im vergangenen Jahr mit dem Gewinn der Deutschen Meisterschaft in der Kategorie „Eigenbau“ ihren (vorlœufigen) Höhepunkt fand.
Der Grundrahmen entstand nach einer originalen Rahmenzeichnung von ÖAF im Maßstab 1:20. Er besteht aus 0,5-Millimeter-Messingblech, welches ich auf meiner kleinen Kantbank zu U-Profilen geformt habe. Die Quertraversen wurden in der Zeichnung ausgemessen, auf den angestrebten Maßstab 1:14,5 umgerechnet, gekantet, verlötet und mit allen aus der Zeichnung ersichtlichen Winkeln und Bohrungen versehen. Aus Ein-Millimeter-Messingblech wurde nun die Verstärkung für die tiefer liegende Schwerlast-Kupplung gebaut und montiert. Aus dem gleichen Material entstanden auch die zwei hinteren Halter für die Pendelachsaufhängung. Nun wurden zwei Dreh- und Fräseteile hergestellt, die zur Aufnahme des Blattfederpakets dienen. Dies entstand aus der Feder einer alten Anwurfvorrichtung eines Rasenmähers. Das einzige Problem war, dass die Federlagen nur schwer zu bohren waren. Schließlich musste jede Lage ein Loch für den Herzbolzen bekommen, der die 18 Lagen zusammenhält. Befestigt werden die Federpakete mit 1,6-Millimeter-Bügeln und Druckstücken. Für die Vorderachsen wurden gemäß der Zeichnung Federböcke gefräst und mit 1,2-Millimeter-Sechskantschrauben an ihrer Position befestigt. Die Weitspaltenfeder hat vier Lagen aus dem gleichen Material wie die an der Hinterachse und drei Lagen aus ABS.
Hinterachse
Die Achsen sollten – wie es sich für ein Eigenbau-Fahrzeug gehört – in meiner Werkstatt entstehen. Also einen Alu-Block genommen und los ging das Bohren, Fräsen und Drehen. Das Ziel war, so kleine Achsen wie möglich zu bauen. Zusätzlich sollte in der Hinterachse eine Differenzialsperre vorhanden sein. Als Antriebszahnräder kommen zwei um 45 Grad schräg verzahnte Zahnräder mit zehn und 25 Zähnen im Modul 0,75 zum Einsatz, im Differenzial werden vier Ausgleichkegelräder mit 20 Zähnen (Modul 0,5) verwendet. Der Differenzialkorb besteht aus Rundmessing. Die Differenzialsperre funktioniert, indem ein Innensechskant (Kopf einer Inbusschraube) einen Sechskant am Differenzialkorb und einen, der mit der Achse verstiftet ist, miteinander verbindet. Geschaltet wird die Differenzialsperre mit einer Schaltgabel die über einen Bowdenzug mit einem Servo verbunden wird. Gelagert sind die Achsen mit vier Kugellagern für die Halbachsen und zwei Kugellagern für die Eingangswelle. Außen auf den Halbachsen sind Mitnehmer aus Messing verstiftet, die Radnaben sind aus Alu gedreht und mit Messing-Drehteilen in Form eines Außenplanetendeckels auf den Halbachsen verschraubt. Die Achsaufhängung entstand nach originalen Fotos, ist aus Messing gefräst und mit 1,6-Millimeter-Stehbolzen zusammengeschraubt. Ein Verdrehen wird durch eine 1,6-Millimeter-Inbusschraube, die in die Achse gedreht ist, verhindert. Die Achsen sollten natürlich auch eine Bremse bekommen, also wurden erst einmal vier Bremstrommeln aus Alu gedreht. An die Achse kamen auf jeder Seite eine Ankerplatte und ein Lagerbock für die Bremswelle inklusive Bremshebel und den Nocken. Der Bremsbelag aus Polyamid sitzt auf einer Seite der Ankerplatte auf dem Nocken und wird auf der anderen Seite von einem kleinen Stift geführt. Die Betätigung der Bremse übernehmen je Achse zwei Druckluftbremszylinder.
Kardanwelle
Die Vorderachse entstand im Mittelteil wie die Hinterachse, allerdings ohne Differenzialsperre. Außen sind 3-Millimeter-Stahlstifte als Achsschenkelbolzen in die Achsfaust eingepresst. Die Halbachsen bestehen aus kurzen 4-Millimeter-Wellen, die mit Mitnehmerstücken für Kugelgelenke versehen sind. Der Achsschenkel besteht aus einem Dreh- und Frästeil aus Messing, an dem die Achssenkellager mit 2-Millimeter-Inbusschrauben befestigt werden.
Der Winkel der Lenkhebel für das Lenktrapez wurde mit einer Pappschablone des Fahrgestells ermittelt. Die Kardangelenkwelle ist aus dem RC-Car-Bereich und wird hoffentlich zuverlässig seinen Dienst verrichten. Die Radnaben sind aus Alu gedreht und mit einem Messing-Drehteil in Form eines Außenplanetendeckels auf der Gelenkwelle verschraubt.
Das Lenkservo wird so eingebaut, dass der Lenkhebel an der Stelle sitzt, an der er auch in einem originalen Lkw montiert ist. Das Servo bekommt ein Gehäuse in Form des Kühlers, letzterer ist mit dem Rahmen verschraubt. Der Lenkhebel ist durch eine Lenkstange mit der ersten Achse verbunden. Eine zweite Lenkstange führt zu einem Zwischenhebel, der vor der zweiten Achse im Rahmen verschraubt ist. Gelagert ist dieser Hebel mit zwei kleinen Kugellagern. Hebel und Lenkhebel der zweiten Achse sind wiederum mit einer Lenkstange verbunden. Die Lenkhebel der zweiten Achse sind um einige Millimeter länger als der der ersten Achse, woraus sich der unterschiedliche Lenkeinschlag der Achsen ergibt.
Zwei Getriebe
Mein Modell funktioniert mit zwei Getrieben. Das Dreigang-Schaltgetriebe funktioniert so, dass ein Servo zum Schalten ausreicht. Funktionsfähig wird das Getriebe durch einen 12-Volt-LRP-Truckpuller. Die Verteilung übernimmt dann das zweite Getriebe, ein Verteilergetriebe mit zuschaltbarem Allradantrieb. Die Zahnräder haben ein Modul von 0,5 und sind gerade verzahnt. Das Schaltgetriebe hat zwei Wellen und funktioniert über zwei Schaltmuffen. Auf der Getriebeeingangswelle befinden sich vier Zahnräder und ein Sechskant-Mitnehmer für die Schaltmuffe. Zwei Zahnräder und der Mitnehmer sind fest mit der Welle verbunden. Die anderen beiden Zahnräder bekommen ein Kugellager und der Bund wurde zu einem Sechskant gefräst, der dann durch eine Schaltmuffe mit dem Sechskant-Mitnehmer verbunden werden kann. Als Schaltmuffe hat sich der Kopf einer Inbusschraube bewährt.
Auf der Ausgangswelle befinden sich drei Zahnräder. Ein festes und zwei mit Sechskant sowie einem festen Mitnehmer, wie es bei der Eingangswelle der Fall ist. Es gibt vier Zahnradpaare: Zum ersten die Eingangsuntersetzung 2:1, 15 Zähne auf der Motorwelle, 30 Zähne fest auf der Eingangswelle. Erster Gang, Untersetzung 3,33:1, 15 Zähne fest auf der Eingangswelle, 50 Zähne schaltbar auf der Ausgangswelle. Zweiter Gang, Untersetzung 1,6:1, 25 Zähne schaltbar auf der Eingangswelle, 40 Zähne schaltbar auf der Ausgangswelle. Dritter Gang, Untersetzung 1,16:1, 30 Zähne schaltbar auf der Eingangswelle, 35 Zähne fest auf der Ausgangswelle. Die Schaltgabeln sitzen lose auf der Schaltwelle und werden durch Federn zur Mitte gedrückt, sodass die beiden Zahnräder des zweiten Gangs durch die Schaltmuffen verbunden werden. Zum Schalten befindet sich zwischen den Schaltgabeln ein fester Mitnehmer. Im ersten Gang schiebt die Schaltgabel die Muffe zum ersten Gang, im dritten Gang schiebt die andere Schaltgabel die Muffe zum dritten Gang. An der Ausgangswelle wird das Getriebe von einem X-Ring, der in einem Halter eingebaut und am Getriebe festgeschraubt ist, abgedichtet. Aufgehängt ist die Motor-Getriebeeinheit durch vier Gummipuffer, die zwischen den Haltern im Rahmen und denen an der Motor-GetriebeEinheit sitzen.
Allradantrieb
Im Verteilergetriebe finden sich zwei Zahnräder, die Untersetzung beträgt 2:1. Die Eingangswelle besitzt 20 Zähne, auf der Ausgangswelle sind es 40 Zähne. Diese ist geteilt, im hinteren Teil ist das Zahnrad mit der Ausgangswelle zur Hinterachse fest verbunden. Nach vorne zur Vorderachse hat das Zahnrad einen 10-Millimeter-Sechskant, in dem zwei Kugellager eingebaut sind. In den Kugellagern steckt die Welle zur Vorderachse, auf der ein Sechskant mit Schaltmuffe verstiftet ist, der zum Einschalten des Allradantriebs dient. Das Verteilergetriebe wird an zwei Haltern befestigt, die in der Mitte zwischen zweiter und dritter Achse mit dem Rahmen verschraubt sind. Aufgehängt wird das Getriebe in vier Gummielementen.
Die Verbindung zwischen den Getrieben und den Achsen besteht aus insgesamt fünf Kardanwellen, die aus Messing gefräst und gedreht sind. Eine Kardanwelle besteht aus zwei Gelenkgabeln mit 4-Millimeter-Bohrung und einer 3-Millimeter-Madenschraube. Den Längenausgleich übernehmen je eine Gelenkgabel mit Innensechskant und eine mit Außensechskant. Die Gabeln sind aus 10-Millimeter-Messing rund gefertigt, wobei der Außensechskant direkt an die Gabel gefräst wurde. Die Hälfte mit dem Innensechskant besteht ebenfalls aus einem Stück, in das der Innensechskant mit einem alten Inbusschlüssel getrieben wurde. Die Verbindung der Gabeln übernimmt ein 6-Millimeter-Messingwürfel mit je einer 3-Millimeter-Silberstahlwelle und einem 1,5-Millimeter-Stahlstift. Der Mittelteil der Kardanwelle ist auf 8 Millimeter abgedreht.
Anbauteile
Zunächst bekam der Rahmen die Kotflügel. Jeder Kotflügel besteht aus zwei Tiefziehteilen, die so zusammengeklebt wurden, dass vier Kotflügel für Zwillingsreifen und zwei für Singlereifen entstanden. Für die Befestigung der Kotflügel wurden Halter mit M1,2-Schrauben am Rahmen fixiert, an denen die Kotflügel mit Klemmbügeln und wiederum M1,2-Schrauben befestigt wurden. Zwischen dem vorderen und hinteren Kotflügel sitzen auf der rechten Seite ein Tank und ein Staukasten, auf der linken Seite der zweite Tank und der Batteriekasten. Die Tanks entstehen aus Messing-Seitendeckeln, die mittels einer selbstgebauten Pressform hergestellt wurden, und einem 0,5 Millimeter starken Messingblech als Außenhülle. Der Tankdeckel wurde aus alten Reifenventilen und Kappen erstellt. Die vier Teile wurden zusammengelötet, lediglich die Rückseite blieb offen, um eventuelle Steuerelemente unterbringen zu können. Die Tankhalter wurden aus Messingprofilen zusammengelötet, an denen die Tanks mit Spannbändern aus Sektflaschenverschlüssen befestigt sind. An die Tankhalter kommt noch die Rückwand des Tanks.
Der Staukasten hat eine große Tür, die durch einen Magneten verschlossen wird. In der Mitte ist ein Einlegeboden, beim Öffnen der Tür wird über einen Mikroschalter die Innenbeleuchtung des Staukastens eingeschaltet. Der Kasten wurde aus 0,5-Millimeter-Messingblech gekantet und verlötet. Das Batteriekastenunterteil besteht ebenfalls aus 0,5 Millimeter starkem Messing und hat einen Deckel, der aus ABS-Platten zusammengeklebt ist. Im Batteriekasten sind zwei kleine Batterieattrappen untergebracht und darunter sind zwei Luftkessel montiert. Hinten auf dem Rahmen ist eine Sattelplatte mit Verschiebeeinrichtung befestigt.
Turbolader
Weil das Modell so originalgetreu wie möglich aussehen sollte, bekam der Elektromotor die Attrappe eines V12-Zylindermotors aus ABS verpasst. Als erstes wurden Motorblock und Ölwanne aus geraden ABS-Platten gebaut, die den Elektromotor verdecken. Oben auf jeder Zylinderreihe sind je sechs Ventildeckel aufgeklebt, die in einer Form tiefgezogen wurden. Vorne im Motor befindet sich ein kleiner Elektromotor, der den Lüfterflügel, der aus Messingblech ausgesägt und gebogen wurde, antreibt. Zwischen den Zylinderreihen vorne und in der Mitte befindet sich die Einspritzpumpe mit den Einspritzleitungen (aus Ein-Millimeter-Aludraht) zu den Zylindern. Die Ansaug- und Auspuffkrümmer bestehen aus 5-Millimeter-Rundmaterial. Auf jeder Seite sitzt ein Turbolader zwischen Auspuff- und Ansaugkanal hinter dem Motor. Als Anbauteile gibt es Lichtmaschine und Anlasser sowie einen Ölfilter und zwei Kraftstofffilter.
Das Fahrerhaus nach dem Vorbild eines MAN F 90 entstand aus 0,5 Millimeter dickem Messingblech. Als Vorbild diente ein Modell von Italeri im Maßstab 1:24, von dem die Maße abgenommen und auf 1:14,5 umgerechnet wurden. Um die Vertiefungen zu bekommen, wurden das Blech mit der Laubsäge ausgesägt, die Innenteile etwas verkleinert und mit 0,2 Millimeter starkem Blech als Hinterlage wieder eingelötet. Teilweise wurden auch Blechstreifen aufgelötet, um alle Höhen und Tiefen des Fahrerhauses nachzubilden. Die Türen und die Dachluke sind zu öffnen. Auf dem Dach finden sich wie beim Original funktionierende Rundumleuchten. Im Inneren der Kabine sitzt der Elektromotor, der über einen Riemen zwei kugelgelagerte Hohlwellen antreibt, auf denen die verchromten Drehspiegel aufgeschraubt sind. Durch die Hohlwelle geht ein Halter, auf dem die Glühlampe befestigt ist. Die Lampengläser wurden aus Plexiglas gedreht, poliert und mit Glühlampentauchlack orange eingefärbt. Die Spannung wird durch einen Festspannungsregler auf 6 Volt für den Motor und die Glühlampen begrenzt. Die Sonnenblende entstand aus einer alten Blende von Wedico. Zusätzlich wurden in die Blende zwei Lampen eingearbeitet und mit einem originalen Halter aus Messing am Fahrerhaus verschraubt.
Das Fahrerhaus ist vorne klappbar mit dem Rahmen verbunden und mit einem Kippzylinder als Arretierung gegen unbeabsichtigtes Zurückkippen versehen. Die hintere Fahrerhaushalterung ist so konstruiert, dass das Fahrerhaus in der unteren Stellung fixiert ist. Die Arretierung wird über Bowdenzüge gelöst, um das Fahrerhaus zu kippen. Das Armaturenbrett und die Türverkleidungen entstanden aus ABS-Platten, um sie so originalgetreu wie möglich wirken zu lassen. Auch der Kontrollleuchtenblock darf nicht fehlen. Darin sind SMD-Leuchtdioden zur Einschaltkontrolle, für die Blinker, Fernlicht, Nebelscheinwerfer, Nebelschlussleuchte und die Rundumleuchte eingebaut. Über zwei kleine Mikroschalter wird beim Öffnen der Tür eine Innenbeleuchtung eingeschaltet. Die Türen werden mit Magneten geschlossen und haben noch eine kleine Kurbel zum Betätigen der Seitenscheiben. Die Sitze wurden noch schön in Farbe gebracht und auf ein Untergestell aus Messing geschraubt. Bei geöffneten Türen machen sie eine wirklich gute Figur.
Schwerlastausrüstung
Hinter dem Fahrerhaus befindet sich der Schwerlastturm, in dem die Elektronik – Fahrregler, Soundmodul, Multiswitch und Empfänger –, der Lautsprecher für das Soundmodul und ein Akku untergebracht sind. Der Turm besteht aus einem Rahmen aus T-Profil, der mit einem Quadratrohrgestell an den Haltern des Fahrzeugrahmens verschraubt ist. In dem Gestell sind zwei Servos eingebaut. Das eine schaltet über einen Dämpfer das Dreigang-Getriebe, das andere Servo ist über einen Umlenkhebel mit dem Verteilergetriebe verbunden und kontrolliert den Allradantrieb. Über zwei Bowdenzüge werden die Differenzialsperren der Hinterachsen geschaltet. Die Servos sind mit Attrappen von Luftfiltern und Hydrauliköltanks aus ABS verkleidet. Auf dem T-Rahmen steckt ein großes geschlossenes Gehäuse mit Lüftungsgittern auf jeder Seite. Oben auf dem Gehäuse sind zwei Arbeitsscheinwerfer aufgeschraubt, auf der Rückseite befindet sich eine Leiter. Zwischen Schwerlastturm und Fahrerhaus sitzen auf der linken Seite Staukästen, in denen Schalter und Sicherung untergebracht sind. Auf der rechten Seite sitzt ein Halter mit Ersatzrad. Zwischen Staukästen und Ersatzrad sind in der Mitte zwei Luftansaugstutzen angebaut. Hinter dem Schwerlastturm befinden sich die Auspufftöpfe, in die Rauchgeneratoren eingebaut sind. Unter dem Schwerlastturm sitzt noch ein Gebläse, das über Rohrleitungen mit der Auspuffanlage verbunden ist. Zusätzlich gibt es auch noch einen Laufsteg, unter dem zwei Steckdosen für den Anschluss eines Zusatzakkus sitzen. Sozusagen der krönende Abschluss.
Nach dem Ende einer langen Bauzeit wurde das Fahrzeug dann auf der Deutschen Meisterschaft 2006 in Osnabrück den vielen anwesenden Modellbauern, Zuschauern und den Schiedsrichtern vorgestellt. Und als Lohn für die vielen Stunden Arbeit prämierte die kritische Jury meinen ÖAF 48.792 mit dem 1. Platz in der Kategorie Eigenbau. Doch trotz dieses großen Erfolges bin ich mit meinem Modell noch nicht ganz zufrieden. Ich werde noch Verschönerungsarbeiten wie zum Beispiel das Aufbringen einiger Aufkleber vornehmen und zusätzlich soll noch eine Ballastpritsche entstehen, die später einen Akku aufnehmen soll.