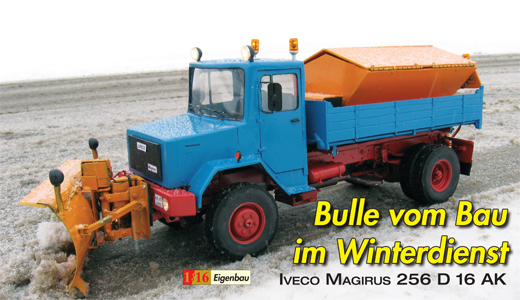
Iveco Magirus 256 D 16 AK
Mein Entschluss, einen Iveco Magirus 256 D 16 AK als Modell in 1:16 nachzubauen, liegt schon gut drei Jahre zurück. Die hierfür benötigten Unterlagen waren beim Hersteller ohne Mühe zu bekommen. Für den Zweiachser mit Dreiseiten-Kipper war eine dreiteilige Kipperspindel schon vorhanden. Mein Sohn hatte diese in seiner Lehrzeit hergestellt. Das Besondere an diesem Modell sollte jedoch seine Verwendung als Schneepflug mit Streuaufsatz sein. Diese Aufgabe nahm das Original lange Jahre im kommunalen Bereich wahr, vor allem bei den Autobahnmeistereien. Viele dieser Fahrzeuge sind mittlerweile allerdings ausgemustert.
Aber auch private Sand- und Kies-Transportunternehmer unterstützten die Kommunen damals tatkräftig beim Schneeräumen, wenn in den Wintermonaten kein Sand gefahren werden konnte. Voraussetzung war aber, dass das Fahrzeug dementsprechend ausgerüstet war: frontseitige Anbauplatte zur Aufnahme des Räumschild sowie zwei Zusatzscheinwerfer am Dach oder an den Holmen der Windschutzscheibe, da die serienmäßigen Scheinwerfer ja vom Räumschild verdeckt werden. Diese Scheinwerfer wurden beim Räumeinsatz abgeschaltet, sodass hier nur noch das Standlicht brannte. Die Fahrbahnausleuchtung übernahmen dann die Zusatzscheinwerfer.
Aufbau
Im Baumarkt erstand ich Alu-U-Profile und fertigte daraus den Fahrgestellrahmen, gerade und ohne jegliche Schweifung. Mit den eingesetzten Traversen erklärt sich auch der Begriff „Leiterrahmen“. Die Vorderachse entstand in eigener Produktion aus Messingmaterial. Für die Herstellung der Federpakete kam eine 2 Millimeter starke Kunststoffplatte zur Verwendung, die in zirka 7 Millimeter breite Streifen geschnitten wurde. Als Zwischenlage sind in jedem Federpaket zwei Lagen Kistenverschlussband aus Stahl eingefügt, welche die Federn etwas härter machen, schließlich bringt der Schneepflug später zusätzliches Gewicht mit ein. Die Hinterachse (Differenzial) stammt, wie immer bei mir, aus dem Hause Wedico. Es ist die schlichte Kunststoffachse. Das Differenzialgehäuse habe ich aber etwas bearbeitet, um seine Klobigkeit zu verringern. Die vier Gehäuseschrauben ersetzten vier M2-Schrauben. Die Hinterachsfedern gleichen in ihrem Aufbau den Federn an der Vorderachse, nur gesellt sich bei ihnen jeweils eine Zusatzfeder hinzu. Der Sinn ist der, dass bei leerem Fahrzeug nur die Hauptfeder an der Federarbeit beteiligt ist und somit der Fahrkomfort erhalten bleibt. Mit zunehmender Ladung allerdings senkt sich der Fahrzeugrahmen und die Federböcke am Hauptrahmen liegen auf den Zusatzfedern auf, wodurch letztere nun auch Federungsarbeit übernehmen und gleichzeitig die Tragfähigkeit der gesamten Federung erhöhen.
Im Antrieb verwende ich ein Eigenbau-Zweigang-Getriebe, dessen Untersetzung 50:1 beziehungsweise 65:1 beträgt. Inklusive der Achsuntersetzung von 2:1 ergibt dies eine Gesamtuntersetzung von 100:1 beziehungsweise 130:1. Geschwindigkeit und Zugkraft sind dadurch ausgewogen, im Räumbetrieb fahre ich aber konstant im ersten Gang. Im Tank, der aus Kunststoff entstand, verbirgt sich der Empfänger. Die Luftkessel wurden aus Blechhülsen, die ehedem kostbare Zigarillos aufnahmen, hergestellt. Für die hinteren Kotschürzen fand wieder Messingmaterial Verwendung.
Das Fahrerhaus
Die vorliegenden Pläne brachte ich mittels eines Kopierers in den Maßstab 1:16. Als Ausgangsmaterial für den Bau des Fahrerhauses verwende ich gern 0,3-Millimeter-Messing- und Kupferblech. Mit einem 100-Watt-Schnelllöter und einem Gaslöter geht es dann zur Sache. Da ich in 25 Jahren Lkw-Modellbau etliche Fahrerhäuser selbst angefertigt habe, besitze ich darin schon etwas Routine. Ich beginne immer mit der Fahrerhausrückwand, danach folgt das Dach. Die Dachrundungen erreiche ich dadurch, dass ich das Material auf der gesamten Breite zirka 6 Millimeter tief einschneide. Der Abstand zwischen den einzelnen Einschnitten beträgt etwa 5 Millimeter. Die Einschnitte werden nun gleichmäßig umgebogen und verlötet. Mit der Feile wird das überschüssige Lot abgetragen, sodass sich alsbald eine kontinuierliche Dachrundung einstellt. Nach derselben Methode entstehen später auch die seitlichen Kotflügelrundungen.
An das Dach schließen sich die seitlichen Windschutzscheibenholme (A-Säulen) an. Man schneidet hierzu zwei Messingblechstreifen nach Plan zurecht. Beide Teile sollten identisch sein. Anschließend werden die Fensterholme an die entsprechende Stelle am Dach angelötet. Eine nicht so ganz einfache Aufgabe, denn zum einen muss das Türmaß eingehalten werden, zum anderen haben die Holme noch einen leichten Winkel nach vorn. Am besten fixiert man den Dachholm mit einem leichten Lötpunkt und korrigiert dessen Sitz, indem man den Lötpunkt leicht teigig erwärmt. Sind beide Holme fixiert, sollten die Türbreiten übereinstimmen. Nicht, dass die Türen unterschiedliche Breiten aufweisen. An die Dachholme wird nun das Vorbaublech angelötet. Vorbaublech, Dachholme und Dach nehmen zum Schluss die Windschutzscheibe auf.
An das Vorbaublech schließt sich dann die Motorhaube an, daran wiederum der Kühlergrill, für den sich ein Lautsprecherschutzgitter hervorragend zweckentfremden lässt. Zum Schluss erstellt man aus Messingblech die beiden Kotflügel. Das Fahrerhaus sollte nun schon recht ansehnlich sein, seine Stabilität erreicht es aber erst, wenn die beidseitigen Einstiege an- und der Fahrerhausboden eingelötet sind. Natürlich darf das Armaturenbrett nicht fehlen. Zum Schluss erstellt man die Türen und die Fahrerhaussitze. Lenkrad und Schalthebel aus Messingrohr und Draht vervollständigen das Fahrerhaus in seinem Innenraum. Mit der Feile wird nun erst das überschüssige Lot abgetragen, danach kommt Spachtelmasse an die Stellen, wo Substanz fehlt. Mit Ausdauer und Fleiß darf geschliffen werden, so lange, bis man mit dem Endprodukt Fahrerhaus zufrieden ist. Mit zwei Stiften vorn unter dem Kühlergrill und zwei hinten unter der Fahrerhausrückwand wird die Kabine auf das Fahrgestell aufgesteckt.
Kipperaufbau
Für den Kipper wird auf den Fahrgestell- ein Hilfsrahmen aufgesetzt, da am Fahrgestellrahmen selbst weder geschweißt noch gebohrt werden darf, um dessen Stabilität nicht zu mindern. Aus einem massiven Messing-Vierkantstab (5 x 5 Millimeter) längt man sich zwei Längsträger ab, die hinter dem Fahrerhaus beginnen und bis zum Fahrgestellende reichen sollen. Drei Traversen aus demselben Material verbinden am Anfang, in der Mitte und am Ende die beiden Längsträger. Man erreicht dies durch Verlöten und/oder durch Verstiften. An den Außenseiten der Hilfsrahmenlängsträger werden vorn, mittig und hinten Messingblechstreifenabschnitte (etwa 10 x 10 Millimeter) angelötet. Legt man nun den Hilfsrahmen auf den Fahrgestellrahmen, umfassen diese die Längsträger des Fahrgestellrahmens und halten den Hilfsrahmen in Position. Bohrt man nun kleine Löcher in die Bleche, lassen sich Hilfs- und Fahrgestellrahmen miteinander verschrauben.
Auf dem Hilfsrahmen werden danach die Kipperlager angebracht. Messingrohr mit einem Durchmesser von 6 Millimeter ist hierzu geeignet. Jetzt ist der Zeitpunkt gekommen, die Kipperbrücke zu erstellen. Eine rechteckige, 2 Millimeter starke Kunststoffplatte bildet den Kipperbrückenboden. Unterhalb werden Längsträger und Traversen (Querträger), ebenfalls aus Kunststoff, eingeklebt. Diese sind notwendig, damit sich die beladene Kipperbrücke beim Ankippen nicht durchbiegt und verwindet. Anschließend werden auch hier Kipperlager aus Messing-Vierkantstäben am Kipperboden so angebracht, dass sie mit denen auf dem Hilfsrahmen exakt korrespondieren.
Abschließend vervollständigt man die Kipperbrücke mit den seitlichen und hinteren Bordwänden. Diese entstehen auch hier aus Kunststoff. Im Prinzip reichen Pendelbordwände eigentlich aus. Das heißt, der Aufbau gestaltet sich dadurch etwas einfacher. Die Bordwände sind dann nur oben zu lagern und unten mit einer drehbaren Welle zu versehen, die auch die Verschlussriegel tragen. Bei Kipperfahrzeugen der älteren Generation, zu denen auch das Vorbild dieses Modells zählt, musste beim seitlichen Kippen von Hand entriegelt werden. Beim Kippen nach hinten geschah dies automatisch. Damit sich die hintere Bordwand beim Ablassen der Kipperbrücke früh genug schließt, noch bevor die Verschlussriegel ihre obere Endlage erreichen, müssen die Pendellager der Bordwand etwas nach vorn (in Richtung Fahrerhaus) versetzt liegen.
Kipperspindel
Vor vielen Jahren hatte Konrad Osterrieter sich die Kipperspindel-Mechanik ausgedacht und in seinen Modellen mehrfach installiert. Heute gibt es diese von einigen Anbietern zu kaufen, allerdings nicht gerade zum Schnäppchenpreis. Die Kipperspindel besteht aus drei oder vier ineinander laufenden Schraubensegmenten (Hülsen mit Innen- und Außengewinde an ihrer Basis). Bauartbedingt können die Segmente beim Herausdrehen nicht auseinanderfallen. Beim Eindrehen allerdings kann es sein, dass sich einzelne Segmente herausdrehen. Durch Einsetzen eines Drahts – beispielsweise einer Büroklammer – in den letzten Gewindegang eines jeden Segments kann dies verhindert werden. Am besten man verlötet den Draht mit dem Gewindegang. Die Aufhängung der Kipperspindel erfolgt mit einer vierfachen Lagerung, die einer kardanischen Aufhängung entspricht. Wie man dies macht, zeigen Bilder besser als viele Worte. Der Antrieb der Kipperspindel erfolgt mit einem kleinen Elektromotor, der über eine Kardanwelle mit Schiebestück auf den einstufigen Schneckentrieb wirkt. An das untere Ende des dicksten Segments ist das Schneckenrad angelötet (30 Zähne), in das die von der Kardanwelle in Drehung versetzte Schnecke eingreift. Die Schnecke selbst wird an der Trägerplatte links positioniert. Angelötete Vierkant-Messingblöcke übernehmen deren Führung und Lagerung. Der Schneckentrieb ist im Modul 0,5 ausgeführt.
Auf Endschalter, die rechtzeitig die Stromversorgung unterbrechen, kann nicht verzichten werden. Diese sind so einzubauen, dass sie schon aktiv werden, bevor die Kipperspindel ihre mechanischen Endanschläge erreicht. Läuft die Spindel unkontrolliert in die obere oder untere Endstellung, benötigt man danach eine Zange, um die einzelnen Segmente wieder frei zu drehen. Die Anschlüsse der Endschalter werden mit Dioden überbrückt, die nach dem Umpolen der Stromversorgung den Kipperspindelantrieb in entgegengesetzte Richtung laufen lassen. Um die Kipperspindel mit Strom zu versorgen, reicht ein elekronischer Umschalter mit Relaisausgang. Mit diesem kann dann per Fernsteuerung ein Ausgang des Fahrreglers auf den Fahr- oder den Kippermotor geschaltet werden. Der andere Ausgang des Reglers bleibt dauernd mit einem Anschluss vom Fahr- und einem Anschluss vom Kippermotor verbunden.
Streuaufsatz
Der Streuaufsatz besteht aus 2 Millimeter starken Polystyrolplatten. Zwei um 45 Grad geneigte Seitenteile werden mit Vorder- und Hinterplatte verklebt. Das Teil sieht nun aus wie ein auf dem Kopf stehendes Hausdach. Seitliche Stützen fixieren diesen Aufbau auf der Grundplatte. Damit das Streusalz bei Regen oder Schneefall nicht feucht wird, werden zwei Abdeckungen angefertigt, die mittels Scharnierband klappbar an dem Streuaufsatz befestigt werden und somit das Ladegut schützen.
Streuantrieb
Zwei elektromotorische Antriebe sind notwendig, um den Streuantrieb zu realisieren. Im Bodenteil des Streuaufsatzes läuft eine Schnecke, die das Streugut nach hinten zum Streuteller befördert. Nach langen Überlegungen, wie solch eine Schnecke selbst angefertigt werden könnte, brachte mir der Besuch eines Baumarkts die rettende Idee. Dort fand ich zirka 30 Zentimeter lange, 15 Millimeter starke Holzschrauben mit Schneckengewinde. Die Schraube wurde von meinem Sohn Matthias auf das richtige Maß gekürzt und vorne auf 4 Millimeter abgedreht. Die Schnecke läuft nun im unteren Bodenbereich im Streuaufsatz. Sie ist vorn in einer Bundbuchse gelagert und wird dort auch per Zahnrad und Getriebemotor angetrieben. Im hinteren Teil übernimmt das Schneckenrohr die Führung. Von dort fällt das Streugut dann in den Streuteller. Dieser besteht aus zwei Kunststoffscheiben mit eingeklebten Zwischenstegen. Durch die Rotation des Streutellers beschleunigen die Zwischenstege das Streugut und katapultieren es in einem kreisförmigen Fächer auf die Straße. Den Antrieb des Streutellers übernimmt ein kleiner Faulhaber-Getriebemotor (i = 41). Dieser sitzt über dem Streuteller und treibt diesen mit einer 2-Millimeter-Welle an.
Der Tag der Erprobung kam und der Testlauf konnte beginnen. Haushaltssalz wurde eingefüllt und dann die beiden Antriebe mit 6 Volt beaufschlagt. Alles klappte auf Anhieb, die Schnecke im Untergrund beförderte das Streugut ins Fallrohr und der Streuteller warf das Salz über die Fahrzeugbreite hinaus auf die Straße. Ich war zufrieden. Über einen separaten Schaltkanal wird der Streuantrieb geschaltet. Davor sitzt allerdings noch ein Schaltkanal, der parallel zum Fahrantrieb des Modells geschaltet ist. Dieser ist so eingestellt, dass er bei Vorwärtsfahrt des Magirus schon durchschaltet, bevor er sich in Bewegung setzt und damit Spannung auf den zweiten Schaltkanal gibt. Klartext: Knüppel leicht nach vorn, es setzt der Streuantrieb ein, das Modell steht aber noch (oder per Schaltkanal wird der Streuantrieb unterbrochen), Knüppel weiter nach vorn, das Modell nimmt langsam Fahrt auf. Steht das Modell, steht auch der Streuantrieb.
Räumschild
Im Fachjargon wird das so genannte Räumschild auch Mehrscharpflug genannt. Die Scharsegmente sind dabei federnd gelagert, sodass diese beim Überfahren von Hindernissen, wie Kanaldeckeln oder Ähnlichem, nach hinten umklappen und danach per Rückstellfeder wieder in die Ausgangsposition zurückschwenken. Pflug und Hindernis überstehen dies auch bei Geschwindigkeiten von bis zu 50 Kilometer pro Stunde schadlos. Mein Pflug besteht aus 0,8 Millimeter starkem Zinkblech. Dieses bog ich mit einer Sprudelflasche in die gewünschte Form. Mittig an der Rückseite wurde dann ein Halter angelötet, der das Drehlager zum Links- und Rechtsschwenken aufnahm. Das Drehlager besteht aus zwei Antennenrohrstücken. Das mittlere Rohr hat eine feste Verbindung mit der Pflugschar. In dieses Rohr habe ich eine Servoverzahnung von einem Servoarm eingelassen. In diese Verzahnung greift nun das Servo und schwenkt das Räumschild (rechts, mittig oder links). Das äußere Rohr des Drehlagers hat oben und unten auf beiden Seiten Lagerbolzen. Die Verbindung zwischen Montageplatte und Pflug erfolgt nun mit einem Parallelogramm. Hierzu fertigt man sich aus Messingflachmaterial (2 x 5 Millimeter) vier gleich lange Teile von je 35 Millimeter. An beiden Enden bohrt man 2,1-Millimeter-Löcher.
Nun befestigt man die Teile erst am Drehlager und später an der Montageplatte. Man hat jetzt einen so genannten Kraftheber, der es ermöglicht, den Pflug anzuheben oder abzusenken. An den beiden unteren Hebern habe ich einen Messing-Vierkant eingelassen, der in der Mitte eine 3-Millimeter-Bohrung besitzt. Ein kleines Miniservo wurde zum Getriebemotor umgebaut und in dem Abtrieb eine 3-Millimeter-Spindel verankert. Die sitzt nun zwischen dem Kraftheber und steuert das Heben und Senken über den darunter befindlichen Messing-Vierkant mit dem M3-Gewinde. Angesteuert wird der Servomotor von einem Minifahrregler. Um das Räumschild nun am Fahrzeug anzubringen, bedarf es einer Befestigungsplatte. Die entstand aus einer Pertinaxplatte mit Kupferbeschichtung. Diese ist mit zwei Schrauben durch die Stoßstange hindurch an der dahinterliegenden Traverse befestigt. Das Räumschild selbst wird nun seinerseits mit zwei M2-Schrauben daran fixiert. Steckverbindungen unterhalb der Stoßstange stellen die elektrische Verbindung sicher. Der Aufbau war nun so weit fertig und wurde getestet. Mit Sand als Räumgut ging es ans Werk. Die Hinterachslast mit Salz als Ladegut war ausreichend und das Modell pflügte sich seinen Weg ohne Traktionsverlust durch den Sand. Der zuvor beschriebene Streueinsatz funktionierte bestens.
Einer nach dem anderen
Somit war nur noch das Problem mit den beweglichen Pflugscharsegmenten zu lösen. Ich entschloss mich, aus 2-Millimeter-Kunststoff eine Verschleißschiene zu erstellen. Diese ist so lang wie der Pflug und 12 Millimeter hoch. Mit Gummistreifen (Fahrradschlauch) und Sekundenkleber wird das Ganze an der Rückseite des Pflugs befestigt. Die Verschleißschiene federt nun bei einem Hindernis nach hinten. Allerdings etwas zu leicht und auf der gesamten Länge. Deshalb klebte ich in der Frontseite des Pflugs noch einen zusätzlichen Gummistreifen ein, gleichzeitig unterteilte ich die Verschleißschiene in mehrere gleich lang Teile und schliff diese mitsamt den Gummistreifen mit der Minitrennscheibe ein. Somit entstanden einzelne, federnd gelagerte Pflugsegmente, die nun einzeln auf das Überfahren von Hindernissen reagieren. Abschließend brachte ich an den äußeren Enden des Räumschilds Positionslampen an, die dem entgegenkommenden Verkehr – nach vorn weiß und nach hinten rot leuchtend – seine Breite signalisieren.
Prinzipiell war ich nun zufrieden mit meinem Modell. Das Räumschild funktioniert tadellos, das Streuen ebenso. Das Fahren mit Räumschild ist allerdings gewöhnungsbedürftig, da es ja um einiges breiter ist als das Fahrzeug selbst. Schnell eckt man dann seitlich irgendwo an und schnell ist ein Fremdschaden verursacht. Es gilt so lange zu üben, bis man sich seiner Sache sicher ist. Am Ende allen Räumens entfernt man mit wenigen Handgriffen die Winterdienstausrüstung und ab geht es zur nächsten Baustelle oder ins Kieswerk zum Sand fahren.
Elektronik
Zu guter Letzt bleibt der Blick darauf, was der Magirus so drunter trägt. Das Modell beherbergt unter der Motorhaube acht Mignon-Akkus mit 2.000 Milliamperestunden. Damit ist eine Fahrzeit von 30 Minuten erreichbar. Schaltkanäle, die sämtlich in Eigenregie auf Lochrasterplatinen entstanden, steuern per Relaisumschaltung Streuantrieb, Hauptscheinwerferumschaltung und bei Rückwärtsfahrt die Unterbrechung der Streufunktion. Zum Abschluss bekam das Modell noch drei Rundumleuchten, zwei hinter dem Fahrerhaus und eine am Heck des Streuaufsatzes. Somit ist das Bild auch von der Beleuchtung her stimmig. Was noch fehlt, ist eine angetriebene Vorderachse. Damit werde ich mich wohl eines Tages befassen, zumal das Zweigang-Getriebe schon einen Abtrieb nach vorn bereitstellt.