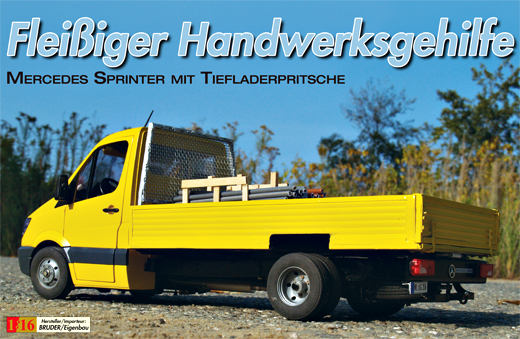
Mercedes Sprinter mit Tiefladerpritsche
Der Sprinter von Mercedes ist für viele Handwerker und Kleinspediteure ein Transporter, ohne den sie ihren Beruf nicht ausüben könnten. Seit Jahrzehnten hat sich dieses Fahrzeug bewährt. Seinen Ursprung hat dieser Transporter im Jahre 1928 als Tempo T 1 Dreirad. Gebaut wurde das Tempo Dreirad von der Firma Vidal & Sohn zunächst in Hamburg-Wandsbek, später folgte dann der Neubau des Tempowerks in Hamburg-Harburg. Gebaut wurde das Dreirad bis 1956, nach dem Krieg kam dann noch der Vierrad-Wagen Matador dazu. Bis 1967 wurden die Tempo-Fahrzeuge gebaut, dann übernahm Hanomag das Tempo-Werk. Die Firma Hanomag wiederum wurde Anfang der 70er-Jahre von Mercedes übernommen. Der Tempo Matador wurde von Hanomag durch die Typen F 20, F 30 und viele andere mehr ersetzt. Als Mercedes das Werk übernahm, bekamen die Hanomag-Fahrzeuge wieder andere Bezeichnungen, an dem Gefährt selbst wurde nichts geändert. Mit dem Typ 207 brachte Mercedes 1975 ein komplett neues Fahrzeug auf den Markt. Denn Mercedes wechselte mit der Einführung des 207 wieder von Front- auf Heckantrieb.
Die Idee dieses Modell zu bauen, war ein spontaner Entschluss auf der Modellbau Schleswig-Holstein im März 2008 in Neumünster. Ein Modellbauer hatte einen Sprinter als fahrfertiges Modell dabei. Dieses war ein Umbau der Firma Tönsfeldt Modellbau. Beim Betrachten des Spielzeugmodells entstand der Plan, einen Sprinter zu einem Pritschenfahrzeug mit niedriger Ladefläche umzubauen. Es sollte ein Fahrzeug werden, das keine extra Funktionen hat. Auch musste nur die Heckklappe zu öffnen sein, wie bei den Tiefladerpritschen üblich. Am nächsten Tag lag ein Sprinter vor mir auf dem Tisch. Die für den Umbau nötigen Reifen und Felgen von WEDICO hatte ich auch gleich geordert. Der Umbau konnte also beginnen.
Teilebeschaffung
Da es für den Sprinter kaum Teile zu kaufen gibt, war Eigenbau angesagt. Es gibt bei Veroma-Modellbau eine Lenkachse aus Kunststoff, die mir aber nicht gefiel. Ein fertiges Hinterachsdifferenzial sucht man bei den bekannten Herstellern auch vergebens. Das Einzige was es gibt, ist ein Miniachsgehäuse im Maßstab 1:16 von AFV-MODEL. Dieses Achsgehäuse passt sehr gut zum Sprinter. Die Lösung von Tönsfeldt mit je einem Motor pro Rad konnte mich aus Scale-Gesichtspunkten nicht überzeugen. Wenn ich ein Modell baue, versuche ich alles so originalgetreu wie möglich zu halten, dazu gehören auch der Rahmen sowie der Antrieb mit Motor, Getriebe, Kardanwelle und Hinterachsdifferenzial. Dass das Achsgehäuse von AFV-MODEL kein echtes Differenzial ist, bedeutet für das Fahrverhalten sowie für die Optik keinen Nachteil.
Den Rahmen wollte ich aus Messing-U-Profilen zusammenlöten. Für die Details besorgte ich mir original Mercedes-Zeichnungen. Als Antriebsmotor sollte ein Faulhaber-Getriebemotor von LEMO-SOLAR zum Einsatz kommen. Nachdem nun feststand, wie der Sprinter aufgebaut werden sollte und die Teile bestellt waren, begann ich damit, den Sprinter zu zerlegen.
Spielzeugdemontage
Zuerst baute ich die Pritsche und die beiden Achsen aus. Dann begann ich, vorsichtig das Fahrerhaus vom Rahmen abzubauen, was gar nicht so einfach ist. Wie bei Bruder üblich, ist auch der Sprinter zusammengesteckt. Die Nasen an den einzelnen Bauteilen sind von außen gar nicht oder nur kaum zu sehen. Das Einfachste war noch, die Türen auszuhängen. Als Nächstes ließen sich die Verkleidungen unter den Türen recht gut ausbauen. Um das Fahrerhaus vom Rahmen zu bekommen, müssen die seitlichen Rammschutzleisten vor und hinter der Tür entfernt werden. Als ich die beiden Rammschutzleisten abgebaut hatte, war das Fahrerhaus an der Rückwand vom Rahmen gelöst.
Nun folgte der schwierigste Teil der Zerlegung: das Abbauen der Stoßstange. Um das Fahrerhaus vom Rahmen zu trennen, muss die Stoßstange abgebaut werden. Dieses Vorhaben war jedoch schwieriger als gedacht − die Stoßstange wollte einfach nicht weichen. Die beiden Nasen, die sichtbar waren, sind leider nicht die einzigen, die sie halten. Mit vorsichtigem Hochdrücken an der Rückwand des Fahrerhauses war auch nicht erkennbar, wo noch Halte-Nasen saßen. Nach stundenlangen Versuchen das Fahrerhaus abzubekommen, versuchte ich es wieder mit vorsichtigem Hochziehen, um einen weiteren Einblick zu erhalten. Und mit einem Mal hatte sich das Fahrerhaus endlich gelöst. Nun waren auch die Nasen zu sehen, die mir diese Probleme bereitet hatten. Sie befinden sich direkt unter den Scheinwerfern. Da der Spalt zwischen der Stoßstange und dem Fahrerhaus sehr eng ist, kann man diese von vorn nicht sehen. Die Stoßstange war jedoch immer noch mit dem Rahmen vereint. Weil sie mich bei den weiteren Arbeiten nicht störte, ließ ich sie zunächst dran. Nachdem nun endlich das Fahrerhaus seinen Widerstand aufgegeben hatte, ließ sich die Inneneinrichtung vom Rahmen gut abnehmen. Dem Umbau stand jetzt nichts mehr im Weg.
Aushöhlung
Als Erstes sollte der Rahmen im vorderen Bereich ausgefräst werden, um Platz für die Achse, den Motor und das Servo zu schaffen. Das Fahrgestell spannte ich mit Abstandshaltern in den Schraubstock meiner Fräse ein. Ohne die Halter wird der Rahmen zusammengedrückt und findet keinen Halt beim Fräsen. Ich begann damit, im vorderen Bereich alles herauszufräsen, was für die Befestigung der Karosserieteile nicht mehr benötigt wurde. So blieben nur die seitlichen Rahmenteile und die vordere Querverbindung für die Befestigung der Stoßstange stehen. Im Bereich der Fahrerhausrückwand blieb ebenfalls die Querverbindung stehen. Hier werden später wieder die Fahrerhausrückwand und die seitlichen Karosserieteile befestigt. Der hintere Rahmen unter der Pritsche blieb zunächst so wie er war. Weil ich die Vorlagen von Mercedes noch nicht hatte, begann ich damit, einen neuen Rahmen zu bauen. In der Breite orientierte ich mich an den Maßen des BRUDER-Modells. Ich nahm zwei U-Profile mit der von mir gewünschten Länge. Um die Profile einbauen zu können, musste ich nun doch den hinteren Rahmenteil ausfräsen. Nachdem das geschehen war, habe ich den Rahmen etwa 10 Zentimeter von hinten mitsamt der hinteren Stoßstange abgesägt. Jetzt konnte ich meine U-Profile mit dem noch vorhandenen Kunststoffrahmen verschrauben.
Rahmen und Achsenbau
Mittlerweile hatte ich das Achsgehäuse von AFV-MODEL erhalten und begann, die Antriebsachse zu bauen. Um aus dem Gehäuse eine funktionsfähige Antriebsachse zu machen, wird ein etwa 10 Zentimeter langes Rohrstück der Maße 5 x 3 Millimeter und je eine Welle mit 2,5 und 3 Millimeter Durchmesser benötigt. Zunächst wird in das Gehäuse links und rechts ein Rohrstück der Größe 5 x 3 Millimeter in der erforderlichen Länge eingelötet. Dabei ist es empfehlenswert, eine 3 Millimeter starke Welle einzustecken, so ist ein einwandfreies Fluchten der Achswelle gewährleistet. Auf die Antriebswelle, auf der das Zahnrad befestigt wird, habe ich vor dem Einbau auf jeder Seite M3-Gewinde geschnitten. Ebenso eine 1,6 Millimeter große Querbohrung für die Mitnahme der Räder. Die Bohrung für das Zahnrad wird erst im Gehäuse gebohrt, wenn das Zahnrad mit dem Ritzel einwandfrei läuft. Für das Ritzel habe ich eine 3-Millimeter-Welle auf einer Länge von 5 Millimeter auf 2,5 Millimeter abgedreht. Im Gehäuse bohrte ich die 2,5er-Bohrung auf 3 Millimeter auf. Die Änderung der Antriebswelle habe ich vorgenommen, weil das Kardangelenk 3-Millimeter-Bohrungen hatte.
Nach dem Einstecken des Ritzels mit der Welle, habe ich von außen auf die Welle einen Stellring mit einer 3er-Bohrung aufgesteckt, um sie zu fixieren. Die Verbindung zur Kardanwelle übernimmt ein Kardangelenk. Als Nächstes wird die Achswelle in das Gehäuse eingesteckt und das Zahnrad an seiner Position fixiert. Nun wird durch den Bund des Zahnrads und die Welle ein Ein-Millimeter-Loch gebohrt und anschließend mit einem Spannstift gesichert. Bei einem ersten Probelauf zeigte sich, dass die Achse bereits sehr leicht lief. Um ein Verschieben der Achswelle zu verhindern, habe ich auf der Welle ein Rohrstück bis zum Anschlag des Achsrohrs aufgeschoben und mit einer Querbohrung von 1,6 Millimeter versehen. Das Rohr hat einen Außendurchmesser von 6 Millimeter, was der Bohrung der Felge entspricht. Durch die Querbohrung habe ich einen Spannstift gesteckt, der als Mitnehmer in die WEDICO-Felge passt.
Die Achse konnte nun eingebaut werden, doch noch fehlte der Rahmen. Weiter ging es mit dem Anfertigen der Rahmenprofile. Ich begann, die Längs- und Querprofile aus 0,7 Millimeter starkem Messingblech zu kanten. Nach dem Vermessen der Vorlagen, die ich mittlerweile auch erhalten hatte, konnte ich die Längsprofile auf die benötigte Länge zuschneiden und an den entsprechenden Stellen einsägen, um den Rahmen im Bereich der Achse zu verjüngen. Die Verjüngung ist für die Zwillingsbereifung erforderlich. Mit den abgelängten Querprofilen wurde der Rahmen zusammengesteckt und dann verlötet. Ein U-Profil am Heck über die gesamte Fahrzeugbreite dient als Rahmenabschluss und zur Befestigung der Rückleuchten. Als Verbindung vom Messingrahmen zum Kunststoffrahmen von BRUDER entschied ich mich für Schrauben. Um eine ausreichende Stabilität zu bekommen, habe ich vom BRUDER-Rahmen etwa 5 Zentimeter stehen gelassen. Der neue Rahmen wurde außen auf den Kunststoffrahmen aufgesteckt und mit sechs Schrauben pro Seite verschraubt. Es folgten nun der Einbau der Hinterachse und des Getriebemotors. Den Motor habe ich hinter der Vorderachse im Rahmen eingebaut. Eine Kardanwelle treibt wie im Original die Achse an.
Gelenkig um die Kurve
Die Lenkachse ist genau wie die von großen Minitrucks aufgebaut. Weil mir die Kunststoffachse von Veroma nicht zusagte, habe ich mir die Lenkachse selbst gebaut. Hierfür habe ich MS-Vierkant-Rohr 6 x 6 Millimeter benutzt. Das Vierkant-Rohr ist wie das Vorbild zur Faustachse gekröpft. Dazu wurde das Rohr auf jeder Seite zweimal eingesägt, gekröpft und verlötet. An den Enden habe ich ein U-Profil aufgelötet. Zur Verstärkung bohrte ich in das U-Profil ein 4-Millimeter-Loch, steckte eine Senkkopfschraube in das Achsrohr und verlötete dies. Ein weiteres U-Profil, das über das an der Achse greift, ist für die Radaufnahme zuständig. Die U-Profile sind senkrecht mit einer 2-Millimeter-Schraube verbunden. Die Schraube wird nur so weit angezogen, dass die äußeren U-Profile leichtgängig sind. An dem äußeren U-Profil ist ein gebogenes Messing-Rechteckrohr der Größe 4 x 2 Millimeter aufgelötet. Das Rechteckrohr dient zur Aufnahme der Spurstange und der Anlenkung des Servos. Für die Radaufnahme ist in dem äußeren U-Profil eine M3-Senkkopfschraube eingelötet, auf die das Rad aufgesteckt wird. Gehalten wird das Rad mit einer Mutter. In den vorderen Felgen sind je zwei Kugellager der Größe 6 x 3 x 3 Millimeter eingepresst.
Die Aufhängung der Achsen am Rahmen geschieht wie beim Vorbild mit Blattfedern. Die einzelnen Federpakete bestehen aus drei Lagen. Die erste Federlage ist aus einem 5 Millimeter breiten Messingstreifen. An den Enden der Messingstreifen habe ich ein 3 x 2-Millimeter-Rohrstück mit einer Länge von 5 Millimeter aufgelötet. Die unteren beiden Lagen sind aus Polystrol geschnitten. Zur Befestigung der Achsen am Rahmen habe ich für die Hinterachse U-Profile angelötet. Vorne sind die U-Profile angeschraubt. An den Achsen ist zur Befestigung der Federn ein Stück Flachmessing aufgelötet, in dem je zwei 2-Millimeter-Bohrungen zum Verschrauben sind. Bei den bisherigen Fahrten hat sich gezeigt, dass die Federung aus Messing und Polystrol ausreichend ist. Selbst im beladenen Zustand biegen die Federn nicht übermäßig durch.
Rahmenaufbau
Um die Pritsche auf dem Rahmen zu befestigen, müssen noch Querprofile angebaut werden. Hier habe ich genau wie beim Original fünf U-Profile auf den Rahmen gelötet. Doch bevor ich diese befestigen konnte, musste ich noch ein breiteres U-Profil einbauen. Weil ich den Sprinter als Tiefladerpritsche geplant habe, die für den Transport von kleinen Baumaschinen ideal ist, hatte ich mir vorgenommen, Auffahrrampen mit an Bord zu haben. Die Rampen sollten dazu dienen, einen Kleinbagger oder ähnliches aufzuladen. Die Rampen sollten unter der Ladefläche eingeschoben werden, um sie Platz sparend mitzuführen. Dazu habe ich wie erwähnt ein breiteres U-Profil gekantet, welches in der Mitte auf dem Rahmen eingebaut ist, in dem die beiden Auffahrrampen liegen. Das U-Profil ist 210 Millimeter lang und 35 Millimeter breit. Die Rampen sind 200 Millimeter lang und 15 Millimeter breit und aus zwei Alublechen zusammengeklebt. An einem Ende der Rampen habe ich ein Alu-U-Profil angeklebt. Mit diesem werden die Rampen in ein weiteres U-Profil, das an der Pritsche unter der Heckklappe angeklebt ist, eingehängt. Das obere Blech ist ein 0,8 Millimeter starkes Riffelblech, das mit einem Ein-Millimeter-Blech verstärkt wurde. Die Rahmenquerprofile zur Befestigung der Pritsche sind bis auf das erste alle seitlich an dem U-Profil und auf dem Rahmen verlötet. Das vordere Querprofil ist durchgängig mit dem Rahmen verlötet. Ein weiteres Anbauteil unter dem Rahmen ist der Reserveradhalter, den ich mir vom Original abgeschaut und genauso nachgebaut habe. Er ist aus einem 3-Millimeter-Rohr als U gebogen an den Rahmen angelötet. Der Halter selbst ist aus MS-Rechteckrohr (4 x 2 Millimeter) zusammengelötet. Hinten am Halter ist ein Rohr in den Abmessungen 4 x 3 Millimeter angelötet, welches auf das 3-Millimeter-Rohr gesteckt wird. Vorne am Halter ist ein MS-Winkel in 5 x 5 Millimeter angelötet. In der Mitte des Winkels habe ich ein 2-Millimeter-Loch gebohrt, durch das eine Schraube in den Rahmen gedreht wird. Nach dem Lösen der Schraube, können der Reserveradhalter nach unten geklappt und das Rad nach dem Lösen der Halteschraube herausgenommen werden. Was bei einem solchen Transporter natürlich auch nicht fehlen darf, ist die Anhängerkupplung, die dem Original in nichts nachsteht. Sie ist wie bei Mercedes üblich an einem separaten Halter, der am Rahmen angelötet ist, angeschraubt. Die Anhängerkupplung ist aus einem MS-Flachstück und einem Stück Rundmaterial zusammengelötet. Der Kugelkopf ist eine VA-Stahlkugel, in die ich ein 2-Millimeter-Loch gebohrt habe, um sie dann mit dem Kupplungshals zu verkleben. Die Anhängerkupplung ist mit vier M1,6-Schrauben am Halter befestigt.
Aufbauarbeiten
Weil mir die Pritsche von BRUDER zu kurz war, habe ich eine neue gebaut. Diese ist 270 Millimeter lang und 148 Millimeter breit. Die Bordwände der Pritsche sind 35 Millimeter hoch und aus zwei Alublechen zusammengeklebt. Der Pritschenboden ist aus einer 3 Millimeter dicken Hartfaserplatte, die auf der Unterseite mit Mahagonifurnier beschichtet ist und auf der Oberseite das Aussehen einer Siebdruckplatte hat. Der Pritschenboden des Vorbilds ist auch mit Siebdruckplatten belegt. Letztere finden im Fahrzeugbau vielseitig Verwendung, weil sie sehr robust und wasserfest sind. Der Pritschenboden ist 270 Millimeter lang und 148 Millimeter breit. Um die Alubordwände besser befestigen zu können, habe ich die Hartfaserplatte mit U-Profilen aus Alu eingefasst. Bevor ich aber die Einfassung auf die Platte stecken konnte, habe ich die Hartfaserplatte im Bereich der Räder ausgeschnitten und zweimal mit Holzschutzlasur gestrichen. Durch das Tieferlegen der Pritsche war es notwendig, den Boden im Bereich der Räder auszuschneiden. Andernfalls würden die Räder am Pritschenboden schleifen. Ein Radkasten aus Alublech verschließt später die Löcher. Nach dem Aufstecken der U-Profile legte ich den Pritschenboden auf den Rahmen und bohrte die Löcher für die Befestigungsschrauben von unten durch die Querprofile in die Bodenplatte.
Nun folgte das Anfertigen der Bordwände. Diese sind aus zwei Aluminiumblechen zusammengeklebt. Das äußere Blech hat ein Wellenprofil, das dem Original ähnlich sieht, innen ist ein glattes Blech dahinter geklebt. Die Einfassung der Bordwände besteht oben wie auch unten aus einem Messing-U-Profil. Vorne und hinten ist ein Aluvierkant der Stärke 4 x 4 Millimeter angeklebt. In dem hinteren Vierkant ist eine 1,6-Millimeter-Bohrung für die Heckklappenverriegelung vorhanden. Die seitlichen wie auch die vordere Bordwand werden nun auf die Einfassung des Pritschenbodens geklebt. Nach dem Aushärten des Klebers habe ich von unten zusätzlich Löcher in die Bordwände gebohrt, in denen ich zur Verstärkung Stifte eingesetzt habe. Die Stifte sind nach dem Aushärten des Klebers glatt geschliffen worden.
Weiter ging es mit dem Fertigstellen und Anbauen der Heckklappe. Für die Heckklappe hatte ich bisher nur die beiden Bleche mit dem oberen und unteren Messing-U-Profil verklebt. Die beiden seitlichen Aluvierkant-Profile mit der Verriegelung mussten noch angefertigt werden. Die Herstellung der beiden 4 x 4-Millimeter-Alustücke war etwas aufwändiger als sie nur abzusägen. In den beiden Profilen ist die Verriegelung der Heckklappe eingebaut. Dazu habe ich zuerst senkrecht ein 1,5-Millimeter-Loch für den Verriegelungsstift gebohrt. Anschließend habe ich auf der Längsseite einen Schlitz von 2,5 x 10 Millimeter gefräst, durch den der Verriegelungsstift mit der Feder eingeführt wird. Damit der Stift und die Feder nicht herausfallen können, wird der Schlitz mit einem Messingstreifen von 4 x 20 x 0,8 Millimeter abgedeckt. In dem Messingstreifen ist ebenfalls ein Schlitz von 1,5 Millimeter gefräst, um den Stift zu betätigen. Der Messingstreifen wiederum wird mit zwei M1,6-Schrauben auf das Aluvierkant geschraubt. Zum Einbau wird der Stift oben zum U gebogen und durch das Loch gesteckt, dann wird von unten die Feder auf den Stift geschoben, dieser dann um 90 Grad gebogen und auf eine Länge von 5 Millimeter abgeschnitten. Abschließend wird der Messingstreifen aufgeschraubt. Nachdem das Aluvierkant mit der Heckklappe verklebt ist, kann sie angebaut werden. Die Heckklappe wird mit zwei Scharnieren am Pritschenboden verschraubt. Die Scharniere habe ich aus Messingstreifen und Rohr selbst gebaut. Die Scharniere sind mit je zwei Schrauben an der Heckklappe und am Pritschenboden angeschraubt. Damit die Verriegelung auch verriegeln kann, ist in dem Vierkant der seitlichen Bordwände das 1,6-Millimeter-Loch schon gebohrt. Durch den Federdruck drückt die Verriegelung selbsttätig in die Bohrung. Zum Öffnen wird der Verriegelungsstift kurz hochgedrückt. Diese doch sehr einfache Konstruktion funktioniert sehr gut.
Die Pritsche war nun fast fertig gestellt, es fehlten nur noch die Radabdeckungen und das Schutzgitter hinter dem Fahrerhaus. Die Radabdeckungen sind aus Aluriffelblech gekantet und verklebt. Der Rahmen des Schutzgitters ist aus 4 x 4 Millimeter-Messing-Vierkant-Rohr zusammengelötet. Auf den Messingrahmen habe ich ein verzinktes Drahtgewebe aufgelötet, das wie im Original ein quadratisches Muster hat. Das Schutzgitter wird in zwei Messing-Vierkant-Rohre der Abmessungen 5 x 5 Millimeter gesteckt, die in den Ecken der Bordwände eingeklebt sind. Das Gitter selbst wird weder eingeklebt noch verlötet und kann jederzeit herausgenommen werden. Bevor ich mit dem Lackieren begann, habe ich die Pritsche auf dem Rahmen verschraubt. Die Schrauben habe ich zuerst durch den Pritschenboden gesteckt und mit Muttern versehen. Die Muttern habe ich so weit festgezogen, bis die Schraubenköpfe mit dem Boden bündig waren. Danach habe ich die Schrauben durch die Bohrungen in den Querprofilen gesteckt und mit einer zweiten Mutter gesichert. Nachdem ich nun die Pritsche aufgebaut hatte, baute ich das Fahrerhaus auch noch provisorisch auf und stellte den Sprinter für seinen ersten Fototermin auf die Räder.
Aus Rot wird Gelb
Die Entscheidung, welche Farbe der Sprinter bekommen sollte, war schnell getroffen: Passend zu meinem Fuhrpark sollte er gelb sein. Ich begann wie immer damit, zuerst den Rahmen zu lackieren. Weil ich bei diesem Fahrzeugrahmen verschiedene Materialien habe, musste ich auch verschiedene Grundierungen nehmen. Die Messingteile habe ich wie gewohnt mit einer Grundierung für Ne-Metalle versehen. Die Kunststoffteile sind mit einer Kunststoffgrundierung gespritzt. Dann habe ich die beiden Rahmenteile wieder zusammengebaut und eine zweite Grundierungsschicht gespritzt. Die Deckschicht erfolgte in Schwarz. Die Grundierung wie auch die Deckschicht des Rahmens habe ich mit der Spraydose lackiert. Jetzt war das Fahrerhaus an der Reihe. Bevor ich die Grundierung spritzte, habe ich das Fahrerhaus mit 400er-Nassschleifpapier für eine bessere Haftung der Farbe angeschliffen. Die Grundierung des Fahrerhauses ist wie schon bei dem Rahmen in zwei Schichten aufgebaut. Die Decklackierung des Sprinters ist wieder mit der Airbrushpistole gespritzt. Die Bordwände der Pritsche sind zweimal mit Haftgrund gespritzt, um dann auch in Gelb zu strahlen. Das Schutzgitter hinter dem Fahrerhaus ist mit Felgensilber lackiert, was den Effekt hat, als wäre es gerade neu verzinkt. Die Auffahrrampen sind in Alunatur geblieben, da hier die Farbe zu schnell abnutzen würde Es werde Licht
Nachdem die Lackierarbeiten abgeschlossen waren, widmete ich mich der Elektrik des Sprinters. Die Elektrik und die Akkus unterzubringen war nicht ganz einfach, weil der Platz dafür sehr knapp ist. Ich wollte nichts unter der Pritsche oder im Fahrerhaus haben, daher blieben nur der Raum unter der Motorhaube und darunter im Rahmen übrig. Den meisten Platz benötigen die Akkus, aus diesem Grund habe ich nur sechs Zellen eingebaut. Der Fahrregler und die Sicherung sind in Hohlräumen hinter den Einstiegen eingebaut. Der Empfänger liegt unter dem Kabinenboden seitlich vom Antriebsmotor. Das Lenkservo ist in der Vorderachse eingebaut. Nachdem die wichtigsten Komponenten verteilt waren, blieb unter der Motorhaube noch ausreichend Platz für die restliche Elektrik. Der Platz reichte sogar noch für eine Beleuchtungsplatine von GEWU. Diese hatte ich ohnehin vorgesehen, wollte sie aber ursprünglich unter den Sitzen einbauen. Hier war aber nicht genug Höhe dafür vorhanden. So wanderte die Platine nun unter die Haube. Die Ansteuerung der Elektrik übernimmt ein Achtkanal-Schalter aus demselben Haus, der jetzt unter den Sitzen seinen Platz eingenommen hat.
Nun galt es, die sehr schön gestalteten Scheinwerfer von BRUDER zum Leuchten zu bringen. Die Gehäuse der Scheinwerfer bestehen aus dem Glas und dem dahinter liegenden, chrombedampften Lampengehäuse. In Letztere habe ich an den entsprechenden Stellen 3 und 5 Millimeter große Löcher gebohrt und mit LEDs bestückt. Für das Standlicht, die Blinker und die Nebelscheinwerfer kommen 3-Millimeter-LEDs zum Einsatz. Das Abblendlicht ist mit einer 5-Millimeter-LED bestückt. Auf der Rückseite des Gehäuses sind die Vorwiderstände angelötet, bevor die LEDs mit der Platine verbunden werden. Durch die vorgegebene Position der LEDs ist die Ausleuchtung genial. Der Einbau der Lampen ist einfach. Sie werden von hinten wieder eingesetzt, sodass die Nasen die Lampen wieder halten.
Die Rückleuchten sind optisch die gleichen wie am Original-Sprinter. Es gibt die Minirückleuchten mittlerweile bei einigen Modellbauherstellern mit und ohne LED-Platine. Ich habe mir die Gehäuse ohne Platine bei Veroma gekauft. Die Bestückung der Lampen mit SMD-LEDs habe ich selbst vorgenommen. Der Einbau in die Gehäuse ist zwar etwas fummelig, aber mit etwas Geduld und Zeit gut zu schaffen. Da die Gehäuse bereits eine eckige Öffnung haben, war es leicht, sie hier einzubauen. Die Öffnungen mussten mit der Feile etwas vergrößert werden, sodass sich die LEDs hineinpressen lassen und nicht mehr verrutschen können. In jedes Gehäuse waren sieben SMD-LEDs einzubauen. Als Anschlusskabel habe ich Litzen von Conrad-Electronic verwendet. Die Litze habe ich vor dem Einbau an die Dioden angelötet. Nachdem alle Lämpchen eingebaut waren, habe ich die für Blinker und die, die rot leuchten, noch mit Glühlampenlack versehen. Dadurch wird die Farbe der Gläser noch verstärkt. Das Anschließen der Lampen an der Platine geschieht mit den farbigen Kabeln von GEWU, für die Beleuchtungsplatinen hatte ich keinen Platz. Das Schalten der Beleuchtung über den Achtkanal-Schalter funktioniert einwandfrei.
Bisher hatte ich sieben der acht Kanäle belegt. Den achten verwendete ich für eine Innenbeleuchtung des Fahrerhauses. Hierfür habe ich über dem Spiegel eine SMD-LED angeklebt. Mit den dünnen Kabeln ist das Anschließen und Verlegen der Leitungen keine Schwierigkeit. Mit den beiden Kabeln für die Innenbeleuchtung habe ich auch gleich das Kabel für die Antenne zum Dach verlegt. Die Antenne für den Empfänger sitzt an der gleichen Stelle, an der beim Vorbild die Radioantenne eingebaut ist. Die Länge der Antenne ist in etwa maßstabsgerecht. Für den Betrieb auf dem Parcours ist die Länge ausreichend. Beim Testen der Beleuchtung leuchtete alles wie erwartet, bis auf die hinteren Blinker, die vertauscht waren. Hier musste ich aber nur zwei Drähte umlöten, und schon war alles richtig. Den Schalter für den Fahrbetrieb oder zum Laden des Akkus habe ich in den Tank eingebaut. Der Schalter ist als Einfüllstutzen getarnt. Der Tank ist ein Kunststoffgehäuse von Conrad, das mit zwei Schrauben an den Rahmen angeschraubt ist. Zum Laden des Akkus sind seitlich unter dem Fahrersitz zwei Ladebuchsen eingebaut.
Ab unter die Haube
Bevor ich das Fahrerhaus wieder zusammengebaut habe, drehte ich etliche Runden, um Störungen zu vermeiden. Erst als ich mir sicher war das alles einwandfrei funktioniert, habe ich den Sprinter wieder zusammengesetzt. Die Front und die Heckscheibe des BRUDER-Sprinters waren in einem Stück gefertigt, ich habe daraus zwei gemacht. Die Frontscheibe habe ich oberhalb der Sonnenblenden abgesägt und wieder eingebaut. Die Heckscheibe stutzte ich so weit, bis sie oben und unten etwa einen Millimeter größer als der Scheibenrahmen war. Seitlich wird die Heckscheibe in eine Führung gesteckt. Den Dachhimmel und die Rückwand unter der Scheibe habe ich mit Stoff verkleidet. Nachdem das Fahrerhaus wieder richtig auf dem Rahmen saß, wurde die Stoßstange wieder angebaut. Sie wird von vorne über einen Falz am Fahrerhaus in die Halterung am Rahmen geschoben, bis sie einrastet. Seitlich und hinten habe ich das Fahrerhaus mit kleinen Blechschrauben mit dem Rahmen verbunden. Die Nasen, die das Ganze vorher zusammengehalten haben, waren bei der Demontage abgebrochen oder durch den Umbau nicht mehr vorhanden.
Zum Abschluss sind die seitlichen Rammschutzleisten wieder aufgesteckt worden. Nachdem ich die Türen mit den Spiegeln und Türverkleidungen wieder zusammengebaut hatte, wurden diese auch wieder eingehängt. Die Dachluke, die bisher nach innen zu öffnen war, hatte ich vor dem Lackieren ausgebaut und die Kanten glatt geschliffen. In die Öffnung habe ich jetzt ein getöntes, transparentes Glasdach eingebaut. Bevor ich die Pritsche wieder aufgebaut habe, habe ich nochmals einige Runden gedreht. Der Aufbau der Pritsche war schnell erledigt, die überstehenden Schrauben wurden abgesägt und glatt geschliffen. Zum Vergleich mit dem Original nahm ich mir meine Prospekte und Zeichnungen noch mal zur Hand. Mit dem Ergebnis war ich sehr zufrieden. Das Einzige was meinem Sprinter fehlte, war der Auspuff. Doch auch hier war schnell eine Lösung gefunden. Zwei 7 Millimeter starke Alurohre und ein 12-Millimeter-Stück Vollalu als Auspufftopf. Mit zwei dünnen Alustreifen als Halter ist der Auspuff am Rahmen aufgehängt. Mit dem Anbauen des Auspuffs konnte der Sprinter seine Arbeit aufnehmen. Mit dem Sprinter hatte ich ein Modell gebaut, das, wie ich eingangs erwähnt habe, eigentlich nicht geplant war. Und doch bin ich mit dem Ergebnis sehr zufrieden.