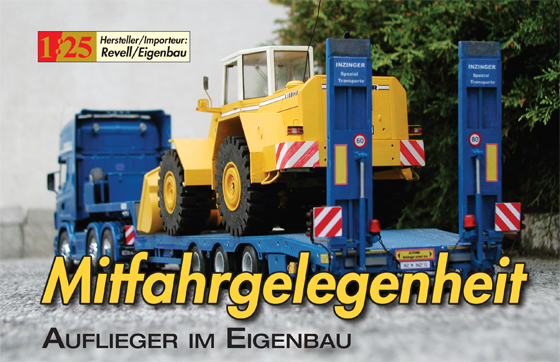
Mitfahrgelegenheit – Auflieger im Eigenbau
Nachdem mein Scania 500 mit seinem Tankauflieger im Maßstab 1:24 schon flott unterwegs war, wollte ich unbedingt einen zweiten Auflieger für interessante An- und Abkuppelvorgänge haben. Die Frage, was für ein Auflieger es werden sollte, klärte sich rasch, nachdem ich meinen selbstgebauten Tieflader samt Zugmaschine an einen Modellbaufreund abgetreten hatte. In meinem Fundus befand sich ein alter Bausatz eines Tiefladers von Revell, der allerdings im Maßstab 1: 25 war. Nach einigen Maßvergleichen kam ich jedoch zu der Überzeugung, dass der Unterschied nicht ins Gewicht fallen würde.
Die Detailplanung war nun der nächste Schritt. Was sollte der Tieflader alles können? Die To-Do-Liste wies folgende Punkte auf: Passender IR-Empfänger zum Scania mit Funktion aller Lichter, ferngesteuerte Aufliegerstützen, ferngesteuerte Rampen und lenkbare Achsen. Damit hatte ich rasch die Vorgaben festgelegt und ich ging ans Werk. Der Rohbau war rasch zusammen geklebt und ich konnte mir über die Ausführung von Lenkung und Achsen die ersten Gedanken machen. Nachdem mein selbstgebauter Tieflader eine Zwangslenkung mit Seilzügen hatte, wollte ich hier einmal eine Lenkung mit Servo und Servotester versuchen.
Gedämpft
Die Achsen habe ich aus 4-Millimeter-Messingrohr gefertigt, die Schwingen bestehen aus 5 x 5-Millimeter-Messing H-Profilen. Die Drehpunkte der Achsschenkel verlegte ich soweit wie möglich in das Innere der Radfelge, um wenig Ausschlag des breiten, doppelbereiften Rads bei Lenkbewegungen zu erreichen. Hergestellt habe ich die Achsschenkel aus Messing-U-Profil und der Lenkhebel besteht aus 0,8-Millimeter-Messingblech. Die Achse ist mit etwas Spiel nur lose durch das H-Profil gesteckt, die Seitenführung der Achse übernimmt der Dreiecks-Lenker von der Schwingenachse. Dieser Aufwand war nötig, da eine feste Verbindung von Achse und Schwinge keine Verschränkung der Achse zulässt. Die Federung besorgen an den abgewinkelten Enden der Achsschwingen eingebaute Federn, die rahmenseitig auf Gummipuffern aufliegen. Die Lenkhebel wurden mit je zwei Löchern versehen, um einen unterschiedlichen Einschlag der Achsen zu erhalten.
Die Lenkstangen habe ich aus 2-Millimeter-Messingrohr und 1,5-Millimeter-Rundmaterial hergestellt. Das Gestänge habe ich zuerst ohne Lötverbindung eingesetzt, die einzelnen Räder genau justiert und erst dann das Gestänge gelötet. Diese Vorgangsweise erleichtert das Einstellen der Räder wesentlich. Die Verbindung vom Lenkgestänge zum Lenkservo stellte ich aus einem Stück Pertinax mit angelötetem Messinghebel her. Durch die nach hinten versetzte Anordnung der Drehachse dieses Verbindungsstücks habe ich den stärkeren Einschlag der kurveninneren Räder pro Achse verwirklichen können.
Verlängert
Jetzt war nur mehr der Verbindungshebel zum Lenkservo herzustellen, um den mechanischen Teil der Lenkung zu komplettieren. Zu diesem Zeitpunkt sah ich beim Durchblättern von TRUCKS & Details das Modell eines ausziehbaren Tiefladers, der mir sehr gefiel. Viele weitere Einsatzmöglichkeiten für den Anhänger wären damit möglich. Doch bei allen Überlegungen das „Teleskopisieren“ zu verwirklichen, war mir meine Achskonstruktion im Weg. Nun, da ein ferngesteuertes Ausziehen oder Einschieben des Anhängers in diesem Maßstab sowieso nicht ohne viel Aufwand möglich ist, kam ich auf die Idee einfach fixe Zwischenstücke einzusetzen. Gesagt, getan. Zuerst kam der große Schnitt, der schon einige Überwindung kostete. Aber mit der kleinen Kreissäge von Proxxon war dieser Schritt schnell getan und schon lag ein zweiteiliger Tieflader vor mir. Ich stellte mir drei Zwischenstücke in verschiedener Länge vor, um den Anhänger in drei verschiedenen Längen fahren zu können. Jetzt kam mir auch die Ausführung der Lenkung mit dem Servotester zugute, da die Verbindung vom Vorderteil nach hinten nur über Drähte erfolgt.
Die Schnittflächen der Tiefladerhälften habe ich mit je einer 2-Millimeter-Polystyrol-Platte abgeschlossen. In der Mitte der Platten sägte ich eine Öffnung von 20 x 12 Millimeter für die Verbindungsstücke ein, links und rechts bohrte ich je ein 2-Millimeter-Loch für die Zentrierbolzen. Hinter den Platten baute ich dann, ebenfalls aus 2-Millimeter-Platten, noch die Aufnahmeschächte für die Verlängerungsstücke. Seitlich erhielten die Schächte noch eine Bohrung mit M2-Gewinde, um die Verlängerungen befestigen zu können. Vorerst stellte ich nur ein zirka 70 Millimeter langes Verbindungsstück her, um die beiden Teile wieder zusammfügen zu können.
Front
Nun kam der Vorderteil an die Reihe. Eine drehbare Pertinax-Scheibe mit 40 Millimeter Durchmesser bildet mit dem Königsbolzen und einem Kunststoffkeil die Verbindung zur Sattelplatte der Zugmaschine. Diese Scheibe erhielt in der vorderen Hälfte sechs Bohrungen für die Empfangsdioden der IR-Übertragung (mit der Schablone der Zugmaschine) sowie links und rechts vom Königsbolzen zwei weitere Bohrungen. Hier setzte ich die Betätigungsstangen für das Lenkpotenziometer aus dem Servotester ein. Das Poti habe ich zwischen den Aufliegerstützen positioniert, sodass ich eine geradlinige Verbindung mit den Betätigungsstangen erreichte. Eine leichte Kröpfung nach außen in Verbindung mit der Elastizität der Stangen ermöglicht einen zerstörungsfreien Knickwinkel der Zugmaschine von über 90 Grad nach links und rechts. Die kleine Platine des SMD-Servotesters von Conrad Electronic habe ich außen am Rahmen befestigt und mit 0,5er-Polystyrol-Platten verkleidet. Zusätzlich habe ich noch ein Potenziometer in Serie zum Lenkpoti vorgesehen, um die exakte Neutralstellung der Lenkung elektrisch einstellen zu können.
Die Abstützungen bestehen aus zwei Zahnstangen-Stücken in Modul 0,5, die den ausfahrbaren Teil bilden und zwei Vierkant-Rohren aus 1,5-Millimeter-Polystyrolstreifen. Diese sind so gemacht, dass sie eine genaue Führung für die Zahnstangen darstellen und an der Oberseite die Lager für die Zahnräder bilden. Auf die Zahnstangen habe ich an der Unterseite noch je einen beweglichen Schuh aus Messing montiert. Eine 1,5-Millimeter-Messingwelle verbindet die beiden Stützen und betätigt über jeweils ein Zahnrad die beiden Zahnstangen. Mit Hilfe eines zweistufigen Schneckengetriebes wurde die Verbindung zum Motor hergestellt. Mit 0,5 Millimeter Messingdraht habe ich die obere und untere Endabschaltung realisiert, wobei sich die untere Endstellung, also die Aufsattelhöhe des abgestellten Aufliegers, durch leichtes Biegen des Kontakts genau justieren lässt. Mit zwei Schrauben habe ich die Stützen befestigt, Motor und Umpol-Relais sind in einen kleinen Rahmen geklebt.
Abgerundet
Nun gefiel mir der eckige vordere Abschluss des Tiefladers nicht so recht, sodass ich diesen einfach mit einer 45-Grad-Schräge gestaltete. Den vorderen Teil der Bordwände habe ich als fix montierte Metallbordwände dargestellt und so Platz für eine Werkzeugkiste und die zwei Reserve-Räder geschaffen. Die Werkzeugkiste enthält neben dem Anhängerakku auch noch den Hauptschalter und das Ladekabel für den LiPo. Die Beschläge sind aus 0,5-Millimeter-Messingblech hergestellt, das Scharnier aus 1,2-Millimeter-Messingrohr und 0,8-Millimeter-Messingdraht. Die Halterungen für die Reserveräder bestehen aus Polystyrolstreifen.
Nun, da das Vorderteil grob fertig war, begann die Aufrüstung des hinteren Teils. Das Heck bekam eine geänderte Abschlussplatte mit neuen Befestigungen für die Auffahrrampen und die Rückleuchten habe ich als Dreikammer-Leuchten ausgeführt sowie mit jeweils drei SMD-LED bestückt. Für eine gute Beleuchtung bei nächtlicher Retourfahrt sorgen zwei superhelle SMD-Leuchten. Links und rechts neben dem Nummernschild habe ich noch eine rote SMD-LED installiert.
On stage
Die Rampen sollten natürlich ferngesteuert funktionieren, den Antrieb dafür stellte ich aus einem zum Getriebemotor umgebauten Mini-Servo von Conrad Electronic her. Das Servo erhielt als Abtrieb eine 1,5-Millimeter-Messingwelle, die am freien Ende in einem Stück Polystyrolplatte gelagert ist. Das auf der Servowelle aufgewickelte „Zugseil“ bewegt einen Schlitten aus Pertinax auf zwei 1,5-Millimeter-Messingstangen. Dieser „Schlitten“ hat links und rechts einen Haken, in die die Seilzüge für die Rampen einhängt werden können. Beide Haken sind verstellbar, um beide Rampen exakt gleich justieren zu können. Diese Art der Befestigung wählte ich, um die Rampen leicht abbauen zu können. Für Ladegut, das per Kran bewegt wird, wollte ich nämlich eine kleine Bordwand als Heckabschluss anfertigen. In der Mitte des Schlittens habe ich eine kleine Zugstange montiert, die beim Absenken der Rampen automatisch die hinteren Abstützbeine in die Arbeitstellung bringt.
Die Abstützrampen habe ich aus den Teilen des Bausatzes zusammengesetzt und aus Alustangen sowie Messingrohr Zylinderattrappen montiert. Zusätzlich habe ich noch Befestigungsmöglichkeiten für Drehlicht und Warntafel vorgesehen. Diese sind elektrisch fest mit dem Anhänger verbunden und können beim Wechsel von Rampen auf Bordwand einfach umgesteckt werden. Die Rampen sind auf einem 2-Millimeter-Messingrohr beweglich montiert und können auf diesen Rohr hin und her geschoben werden. Der untere Lagerbock der Hubzylinder umfasst mit seiner Befestigung die innere Lasche der Rampe und wird damit automatisch mit bewegt. Als Abstützung für den Lagerbock dient eine Gleitfläche an der Heckwand des Aufliegers. Die Rampenbetätigung im Modell erfolgt durch eine vorgespannte Feder zwischen Lagerbock und Rampe. Das Absenken erfolgt durch den Servoantrieb, den Gleitschlitten und das eingehakte Zugseil über eine Umlenkrolle im Lagerbock und schließlich durch das Messingrohr der Hubzylinder.
Leuchtstoff
Der Befestigungsbolzen für die Rampen wird nun durch die 2-Millimeter-Rohre geschoben. Diese Art der Konstruktion ermöglicht ein seitliches Verschieben der Rampen für unterschiedliche Spurweiten der Beladung und eine leichte Demontage, um auf Bordwand umrüsten zu können. Die hintere Bordwand entstand aus Polystyrol, wieder mit den Befestigungsmöglichkeiten für die Warnschilder und die Drehleuchten. Um für den Transport von überbreiten Fahrzeugen gerüstet zu sein, habe ich für eine Verbreiterung noch 3-Millimeter-Löcher in die Seitenwände gebohrt und in diese entsprechende Alurohr-Stücke eingeklebt. Diese sollen dann die Verbreiterungsteile aufnehmen.
Jetzt ging es aber an die Elektronik und die Verkabelung. Begonnen habe ich mit dem Akku in der Werkzeugkiste. Darunter liegend montierte ich einen 5-Volt-Spannungsregler. Danach habe ich die gleiche IR-Empfangsplatine wie im Tankauflieger gebaut und hinter dem Königsbolzen befestigt. Nächster Schritt war die Verkabelung der IR-Empfangsdioden mit der Platine. Die seitliche Beleuchtung habe ich mit Plättchen aus 0,5-Milllimeter-Polystrol und eingeklebten SMD-LED realisiert. Dabei habe ich zuerst die Plättchen mit dem passenden Loch für die LED versehen, diese aufgeklebt, die LED mit Anschlussdrähten versehen und erst dann in die Löcher geklebt. Im hinteren Teil der Ladefläche habe ich beidseitig noch ein kleines Bedienfeld eingebaut. Die Hebel entstanden aus Spritzlingsresten, die grüne LED signalisiert die eingeschaltete Betriebsspannung des Anhängers. Weiter habe ich noch eine Unterspannungsplatine von Conrad Electronic für die Kontrolle des LiPos eingebaut. Auf einem Anzeigefeld links vorne am Anhänger wird dem Fahrer mit einer roten LED beginnende Unterspannung angezeigt. Im Original kann der Fahrer im Rückspiegel Betriebszustände des Anhängers kontrollieren. Im Modell zeigt dieses Kontrollfeld Unterspannung, Lenkung per Handsteuerung oder automatisch und die Aktivierung des Zusatzkanals der IR-Übertragung an.
Selfmade
Als nächsten Schritt fertigte ich die vier Warntafeln mit Beleuchtung an. Da ich nur 1,5-Millimeter-Leiterplattenmaterial zur Hand hatte, kam ich auf die Idee, Ein-Millimeter-Polystyrolplatten mit Kupferfolie zum Aufkleben zu versehen und auf diese dann die jeweils drei weißen und drei roten SMD-LED aufzulöten. Prädikat: nicht empfehlenswert. Eine endlose Fummelei bis diese 24 SMD-LED, noch dazu in der Größe 1,2 x 0,8 x 0,8 Millimeter, „leuchtfähig“ montiert waren. Das nächste Mal wäre mir die Besorgung von dünnerem Leiterplattenmaterial nicht zu viel. Da diese Warntafeln nun endlich fertig waren, erhielten sie noch einen quadratischen Befestigungsbügel aus 1 x 1-Millimeter-Messing, die Anschlussdrähte und ich konnte sie in den vorgesehenen Konsolen montieren und anschließen. In dem ebenfalls 1 x 1 Millimeter großen Loch kann man sie nun bei Bedarf zirka 15 Millimeter herausziehen. Lohn der Mühe ist der Effekt der Beleuchtung, der dem Vorbild doch recht nahe kommt. Die Drehleuchten bestehen aus orangen 3 Millimeter LED. Die Sockel habe ich aus schwarzem Kunststoff gedreht, die Abdeckungen aus Plexistäben mit 6 Millimeter Durchmesser.
Es folgte dann die Montage der seitlichen LED am hinteren Teil des Tiefladers, anschließend die Verkabelung der gesamten Beleuchtung bis zum neunpoligen Verbindungsstecker. Die Drehleuchten erhielten je einen Vierkanal-Blinkschalter von Conrad Elektronik. Beide arbeiten mit leicht unterschiedlicher Taktfrequenz. Die Drehleuchten sind mit eingeschaltetem Hauptschalter in Betrieb. Der Rampenantrieb wird mit einer zum Fahrregler umgebauten Servoelektronik betrieben. Auf den Fotos erkennt man das herausgeführte Potenziometer zur Einstellung der Neutralstellung. Mit dem Einbau von drei Steuerrelais und der Verbindung des Lenkservos zum Stecker war der hintere Teil elektrisch fertig, bis mir noch eine kleine IR-Steuerung aus einem 1:87-Spielzeug-Lkw in die Hände fiel und diese auch noch eingebaut wurde.
Da nun beide Teile fertig verkabelt waren, stand einer Erstinbetriebnahme nichts mehr im Wege. Schnell fertigte ich noch ein neunpoliges Verbindungskabel, baute den Akku ein und als Erstes kam der Test der IR-Verbindung an die Reihe. Diese funktionierte auf Anhieb und nach einigen Justierarbeiten der Endschalter und der kleinen Handsteuerung hatte ich alle Funktionen so wie geplant realisiert.
Inbetriebnahme
Nach dem Ankuppeln der Zugmaschine sind bei eingeschaltetem Auflieger sofort alle Lichtfunktionen in Betrieb. Auf jeden Fall leuchtet bei der Zugmaschine beim Rückwärtsfahren der Rückfahrscheinwerfer. Sobald die Sattelkupplung richtig eingerastet ist, leuchten nun auch beim Auflieger die Rückfahrscheinwerfer. Das ist zugleich die Kontrolle des Kuppelvorgangs. Nun wird bei der Zugmaschine der IR-Zusatzkanal betätigt (beim Scania ist das zugleich die Fahrerhausinnenbeleuchtung) und im Auflieger wird bei der Kombination Zusatzkanal plus Blinker rechts oder links die Abstützung ein – oder ausgefahren. Die Aktivierung des Zusatzkanals wird am Kontrollfeld links vorne am Auflieger durch eine orange LED angezeigt.
Nun zu der Funktion der kleinen IR-Fernsteuerung: Der kleine Handsender hat vier Tasten, die beim 1:87-Modell für Fahrt vorwärts-rückwärts und für Lenkung links-rechts vorgesehen waren. Diese Funktionen habe ich umgelegt auf: manuelle Lenkung des Tiefladers und auf die Rampenbetätigung. Mit den ersten beiden Tasten kann ich von Automatik- auf Handbetrieb umschalten. Im Automatikbetrieb wird der Auflieger von der Zugmaschine zwangsgelenkt, die beiden anderen Tasten der Fernbedienung dienen als Rampenbetätigung. Im Handbetrieb dienen diese Tasten zur manuellen Lenkung des Aufliegers. Die Verknüpfung dieser Funktionen habe ich relativ einfach mittels dreier Relais erreicht. Dieses Feature ist für enge Passagen im Kriechtempo gedacht. Oder man „erfährt“ den Unterschied zwischen gelenkten und ungelenkten Achsen. Ein kleiner Nachteil soll allerdings nicht verschwiegen werden: Bei Fahrt mit aktiviertem Zusatzkanal sollte man den Blinker besser nicht betätigen, da sonst eventuell die Abstützung ungewollt betätigt wird.
Finishing
Nun konnte ich noch die Kleinigkeiten, die das Modell erst richtig beleben, anfertigen. Schutzbleche für die Rückleuchten aus 0,3-Millimeter-Messingblech, einen Unterfahrschutz hinter der letzten Achse mit einem Bedienpult für die Rampen, Unterlegkeil und einen Werkzeugkasten auf jeder Seite. Am Vorderteil waren noch die Schlitze für die Befestigung der Bordwände des Bausatzes vorhanden. Hier muss ich zugeben, dass die Bequemlichkeit mich verleitete, dies für die modifizierten Bordwände zu nutzen. Letztere habe ich noch mit Rungen versehen und sie können bei Bedarf einfach eingesteckt werden. Eine simple Lösung, aber im Nachhinein wären mir Scharniere lieber gewesen.
Jetzt konnte endlich die Lackierung erfolgen. Diese habe ich einfach gepinselt. In dieser Baugröße und bei einem Nutzfahrzeug finde ich das durchaus vertretbar. Nachdem der Anhänger endlich in der gleichen Farbe wie sein Zugfahrzeug vor mir stand, konnte ich mich an die Herstellung der Zwischenstücke machen. Das erste Zwischenstück für die einfache Verbindung beider Teile war ja schon eingebaut. Das zweite sollte eine Verlängerung der Ladefläche um 45 Millimeter bewirken – soviel, dass ich eine Radmulde für den Transport von Lkw realisieren konnte. Die Gesamtlänge der Ladefläche reicht so bequem für einen dreiachsigen Lkw. Die Herstellung erfolgte mit Polystyrol-Platten und einem Reststück geriffelter Platte aus dem Bausatz.
Nach Montage der seitlichen Begrenzungs-LED am Unterfahrschutz fehlte nur noch das durchgehende Verbindungskabel, welches für die Versorgung der seitlichen LED einfach mit einem Vorwiderstand „angezapft“ wurde. Das dritte Zwischenstück sollte nun für den Transport von richtigem Langgut, wie zum Beispiel eines Handymasts geeignet sein. Die Herstellung erfolgte wieder aus Polystyrol-Platten. In der Mitte des Zwischenstücks baute ich noch einen Tisch, der für zusätzliche Befestigung des Ladeguts genutzt werden kann und außen die Warnstangen aufnimmt. Dieser Tisch hat zusätzlich zu den seitlichen orangen LED noch vorn eine weiße und hinten eine rote LED an jeder Außenseite. Verwendet habe ich wieder SMD-LED, der Anschluss erfolgte so wie beim zweiten Zwischenstück. Für den sicheren Transport solch langer Gegenstände habe ich noch zwei Aufsätze aus Messingprofilen hergestellt. Die Aufsätze gleichen die unterschiedliche Ladeflächenhöhe aus und sind mit verstellbaren Rungen ausgestattet.
Multi-Tasking
Als letztes fehlten nun die Verbreiterungsteile. Diese habe ich ebenfalls aus Polystyrol gebaut. Da diese Teile Holzbohlen darstellen sollen, habe ich der Oberfläche mit rauem Glaspapier eine Holzmaserung aufgezwungen. Nach dem Streichen und ein wenig Alterung mit verschiedenen Braun und Grautönen sieht es täuschend echt aus. Die Teile habe ich mit 2-Millimeter-Zapfen versehen, die einfach in die vorgesehen Alu-Rohre eingeschoben werden. Die unterschiedliche Länge der Zapfen ergab sich aus dem jeweiligen Platzangebot hinter den Seitenwänden.
In Ergänzung mit dem Tankauflieger bieten sich für den Scania 500R schon eine Menge an Transportaufgaben. Die aus einfachen Mitteln realisierte IR-Übertragung funktioniert tadellos und bietet ein vorbildgetreues An- und Abkuppeln beider Auflieger ohne mit der Hand eingreifen zu müssen. Die verschiedenen Längen- und Breitenvarianten des Tiefladers erlauben eine Vielzahl von verschieden Transportaufgaben und ergeben einen hohen Spielwert, vor allem in der langen Ausführung mit der Möglichkeit der manuellen Aufliegerlenkung.